Inspection of Wind Turbines
Wind turbines represent a significant investment and require regular monitoring to maintain stable operation. Drones, with their agility and high-resolution cameras, are capable of conducting thorough inspections, identifying minor damages early on, and ensuring the stability of wind farms.
Painpoints
Advantages
Wind power plants cover extensive areas and are widely dispersed, making centralized management challenging.
Enhance inspection efficiency by surveying vast areas and inspecting multiple wind turbines in a single drone flight.
Traditional inspection methods are either hazardous or inefficient, leading to less frequent inspections and potential losses in power generation.
Reduce personnel risk without sacrificing the quality of inspections.
Emerging trends, such as offshore wind power, pose even greater challenges for manual inspections.
Offer adaptable, dependable, and maneuverable drone solutions suitable for various environments.
Solution
Reliable and High Performance Inspection
Multipurpose Drone Inspection
Portable Quick Assessment Inspection
Reliable and High Performance Inspection
The DJI Matrice 30 Series delivers portable yet robust performance, featuring an extended flight range of up to 15 km and ingress protection to endure harsh weather conditions. It accurately detects blade cracks or damage using high-resolution visual and thermal (M30T) sensors, dual-control operations, and precise re-shooting capabilities.
The drone is foldable, portable, and can be easily transported for field operations.
Rapid deployment, operational within 2 minutes.
Laser rangefinder to accurately locate wind turbine defects and obtain coordinates for targeted repairs.
Low-light mode ensures detailed image capture even in poorly lit conditions.
Drone Platform
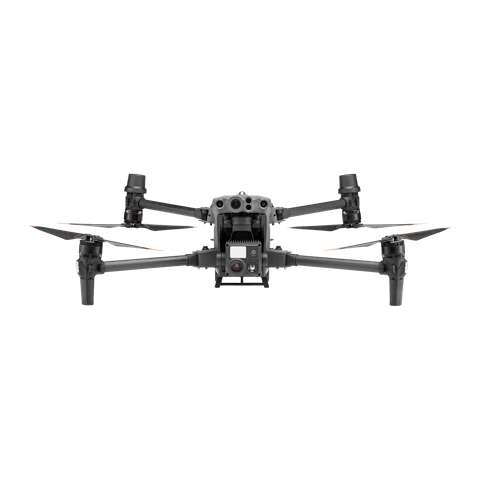
Matrice 30 Series
... Open
Weight (incl. two batteries): 3770 ± 10 g.
Max Flight Time: 41 min.
Sensing system: Six-directional sensing and positioning.
Environment Adaptability: Max Service Ceiling Above Sea Level (without other payload) 7,000 m (with 1676 propellers); Max Wind Resistance 12 m/s.
Zoom camera: 1/2-inch CMOS, Effective pixels: 48MP.
Max Flight Time: 41 min.
Sensing system: Six-directional sensing and positioning.
Environment Adaptability: Max Service Ceiling Above Sea Level (without other payload) 7,000 m (with 1676 propellers); Max Wind Resistance 12 m/s.
Zoom camera: 1/2-inch CMOS, Effective pixels: 48MP.
Workflow
- Mission Planning:
- Fly manually using the DJI Pilot 2 app capturing High-Resolution Images of the key inspection points of the turbine. - Data Analysis:
- Analyze the images to detect defects or required maintenance work by manually reviewing the data collected. Transfer the data to a third-party sofware to identify equipment defects using model detection.
Multipurpose Drone Inspection
The DJI Matrice 350 RTK is a dependable platform with interchangeable payloads tailored to meet the specific needs of each task. Whether for mapping or inspection, the Matrice 350 RTK provides comprehensive operational capabilities for inspection teams.
With its array of payloads, the drone ensures operational efficiency and enhanced inspection capabilities.
Automates inspections and reduces inspection times to as little as 15 minutes per turbine.
Offers longer flight time for prolonged operations.
When paired with the Zenmuse P1, it enables the capture of detailed images for accurate detection of blade damage.
When paired with the Zenmuse H30, it provides high-definition zoom and laser rangefinder capabilities, along with intelligent precise re-shooting functionality, greatly enhancing the efficiency of aerial inspections.
Drone Platform
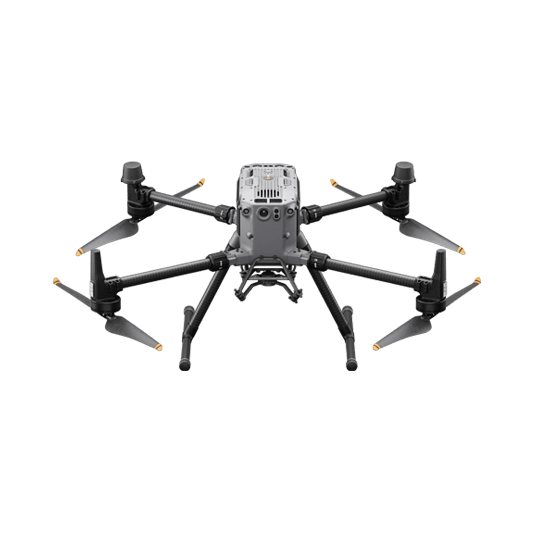
Matrice 350 RTK
... Open
Weight: Approx. 6.47 kg(with single downward gimbal and two TB65 batteries).
Max Flight Time: 55 minutes.
Sensing system: Six-directional sensing and positioning.
Environment Adaptability: IP55, Max Service Ceiling Above Sea Level 7,000 m (with 1676 propellers,without other payload); Max Wind Resistance 12 m/s.
Max Flight Time: 55 minutes.
Sensing system: Six-directional sensing and positioning.
Environment Adaptability: IP55, Max Service Ceiling Above Sea Level 7,000 m (with 1676 propellers,without other payload); Max Wind Resistance 12 m/s.
Payload And Software
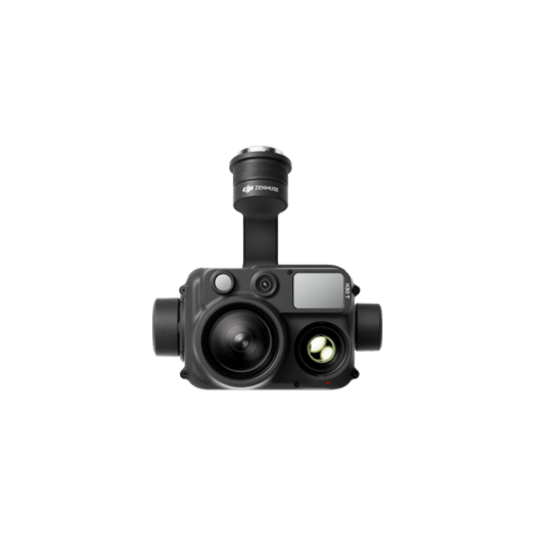
Zenmuse H30T
... Open
Weight: 920±5 g.
Ingress Protection Rating: IP54.
Zoom Camera: 1/1.8-inch CMOS, Effective Pixels: 40 MP.
Wide-Angle Camera: 1/1.3-inch CMOS, Effective Pixels: 48 MP.
Infrared Thermal Camera: 1280×1024@30fps.
Laser Range Finder: max range 3000 m.
Ingress Protection Rating: IP54.
Zoom Camera: 1/1.8-inch CMOS, Effective Pixels: 40 MP.
Wide-Angle Camera: 1/1.3-inch CMOS, Effective Pixels: 48 MP.
Infrared Thermal Camera: 1280×1024@30fps.
Laser Range Finder: max range 3000 m.
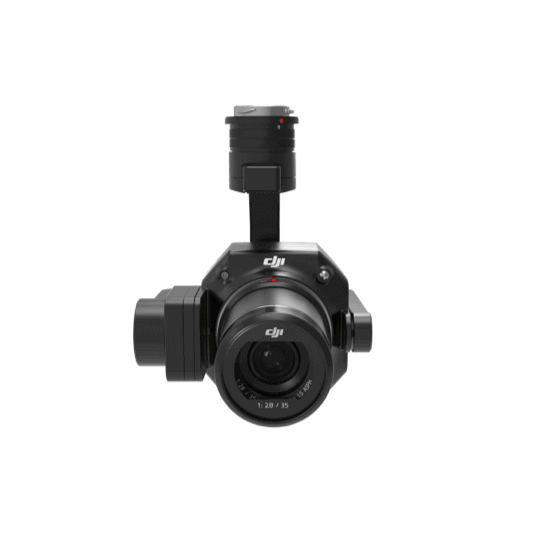
Zenmuse P1
... Open
45 MP Full-frame camera.
Global Mechanical Shutter Shutter Speed 1/2000 Seconds.
3-axis Stabilized Gimbal Smart Oblique Capture.
Global Mechanical Shutter Shutter Speed 1/2000 Seconds.
3-axis Stabilized Gimbal Smart Oblique Capture.
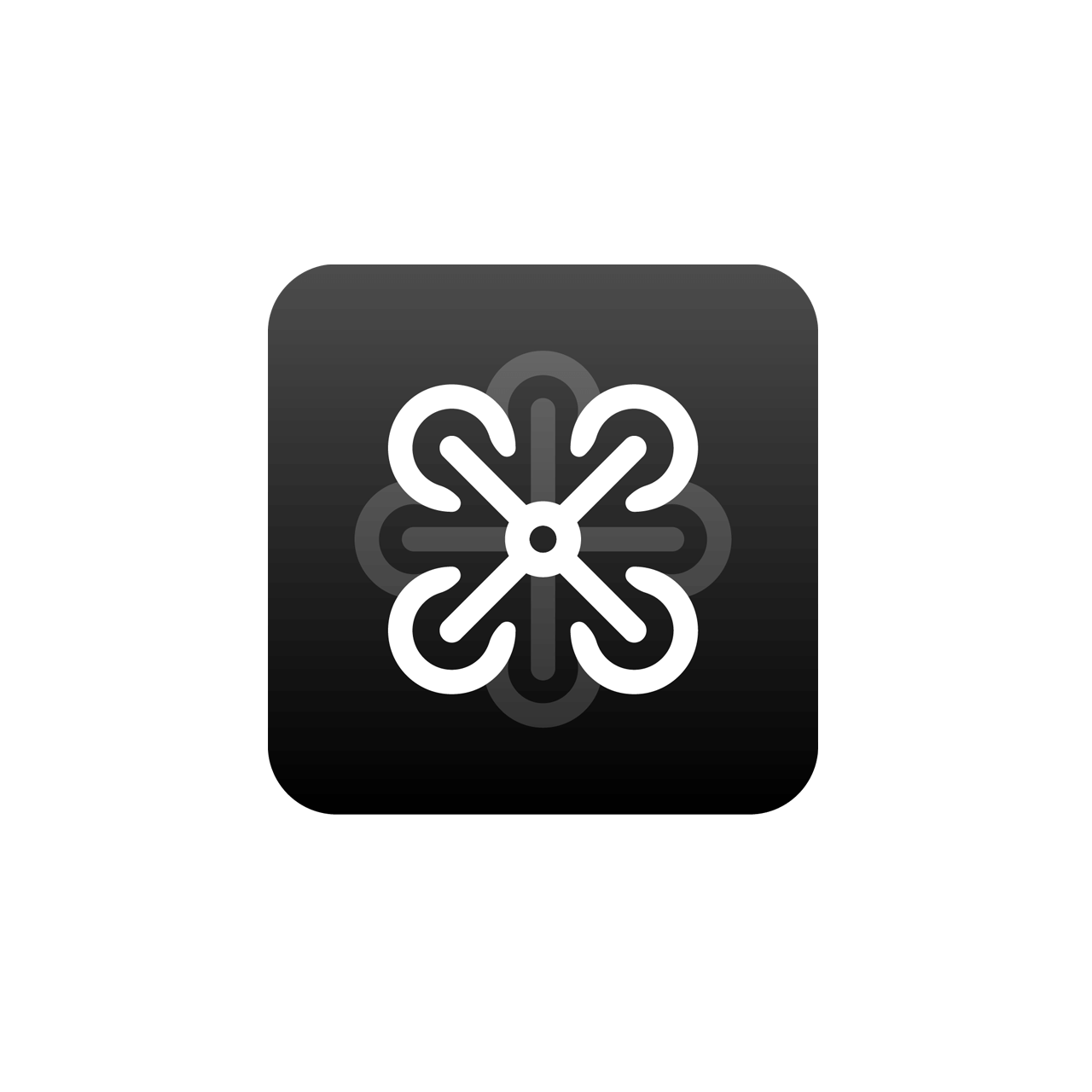
Third-Party Software
Workflow
- Data Collection:
- Use the Matrice 350 RTK equipped with the Zenmuse P1 or the Zenmuse H30 to perform a high-resolution visual inspection using a third-party software. - Data Analysis:
- Analyze the inspection photos manually or use model detection to identify defects on the blades.
Portable Quick Assessment Inspection
The DJI Mavic 3E drones are compact and easily transportable, ideal for rapid inspections. Equipped with high-definition wide and zoom cameras, they provide the perfect solution for swiftly obtaining aerial views for a prompt evaluation of wind turbine conditions
The compact size and maneuverability of the drone allow for close proximity, providing better shooting angles.
Quick deployment and user-friendly operation enable fast assessments of facility infrastructure and equipment.
High-resolution visual sensors capture high quality images, identifying defects that may be easily overlooked by the human eye.
Drone Platform
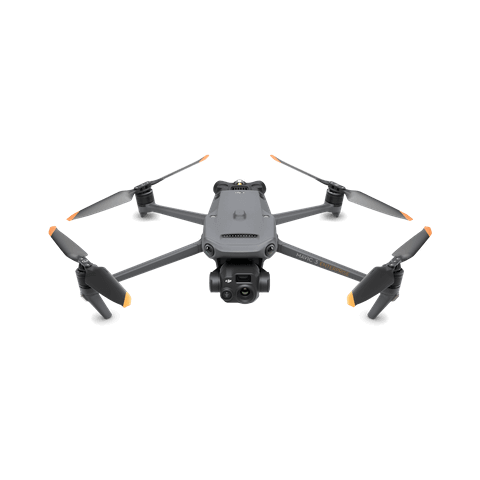
DJI Mavic 3T
... Open
Weight: 920 g
Max Flight Time (no wind): 45 mins
Sensing type: Omnidirectional binocular vision system, supplemented with an infrared sensor at the bottom of the aircraft
Environment Adaptability: Max Take-off Altitude Above Sea Level 6000m; Max Wind Speed Resistance 12 m/s
Wide Camera: 1/2-inch CMOS, Effective pixels: 48 MP
Tele Camera: 1/2-inch CMOS, Effective pixels: 12 MP
Thermal Camera: Video Resolution 640×512@30Hz
Compatible with RTK module and DJI Cellular module
Max Flight Time (no wind): 45 mins
Sensing type: Omnidirectional binocular vision system, supplemented with an infrared sensor at the bottom of the aircraft
Environment Adaptability: Max Take-off Altitude Above Sea Level 6000m; Max Wind Speed Resistance 12 m/s
Wide Camera: 1/2-inch CMOS, Effective pixels: 48 MP
Tele Camera: 1/2-inch CMOS, Effective pixels: 12 MP
Thermal Camera: Video Resolution 640×512@30Hz
Compatible with RTK module and DJI Cellular module
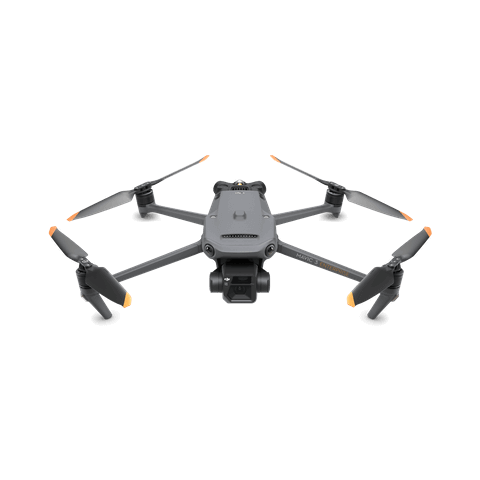
DJI Mavic 3E
... Open
Weight: 915 g.
Max Flight Time (no wind): 45 mins.
Sensing type: Omnidirectional binocular vision system, supplemented with an infrared sensor at the bottom of the aircraft.
Environment Adaptability: Max Take-off Altitude Above Sea Level 6,000 m; Max Wind Speed Resistance 12 m/s.
Wide Camera: 4/3 CMOS, Effective pixels: 20 MP.
Mechanical Shutter: 8-1/2000 s, supports rapid 0.7-second interval shooting.
Compatible with RTK module and DJI Cellular module.
Max Flight Time (no wind): 45 mins.
Sensing type: Omnidirectional binocular vision system, supplemented with an infrared sensor at the bottom of the aircraft.
Environment Adaptability: Max Take-off Altitude Above Sea Level 6,000 m; Max Wind Speed Resistance 12 m/s.
Wide Camera: 4/3 CMOS, Effective pixels: 20 MP.
Mechanical Shutter: 8-1/2000 s, supports rapid 0.7-second interval shooting.
Compatible with RTK module and DJI Cellular module.
Workflow
- Data Collection:
- Fly manually using the DJI Pilot 2 app capturing High-Resolution images of the key inspection points of the turbine. - Data Analysis:
- Analyze the images to detect defects or required maintenance work by manually reviewing the data collected. Transfer the data to a third-party software to identify equipment defects using model detection.