Pipeline Inspection
Oil fields feature numerous pipelines across diverse terrains, which are vulnerable to environmental factors. Remote locations complicate on-site inspections and pose safety risks. Utilizing drones equipped with visible light and thermal cameras for automated inspections can effectively mitigate these challenges.
Painpoints
Advantages
Pipelines often stretch across long distances in challenging terrains, rendering manual inspections hazardous and expensive.
Drones can swiftly cover extensive pipeline corridors, enhancing inspection efficiency without subjecting personnel to unnecessary risks.
Corrosion is a significant concern for pipelines, necessitating regular inspections to assess the structural integrity and detect potential leaks.
Increase the frequency and quality of inspections with pre-planned and repeatable drone-based inspections.
Traditional inspection methods struggle to maintain accurate documentation of changes due to external or environmental factors.
Digitize your inspection records with drone data that is easily stored and shared.
Solution
Portable Pipeline Inspection
Reliable Performance Inspection
Leak Detection Inspection
Automated Routine Inspection
Portable Pipeline Inspection
The compact and portable DJI Mavic 3T, outfitted with high-performance visible light and thermal imaging cameras, is ideal for comprehensive pipeline inspections.
This solution is compatible with the DJI Cellular module[1], which provides 4G-enhanced image transmission, thereby extending its effective operating range in complex urban or mountainous terrains.
This solution is compatible with the DJI Cellular module[1], which provides 4G-enhanced image transmission, thereby extending its effective operating range in complex urban or mountainous terrains.
Compact and lightweight, it is easy to transport and carry.
4G-enhanced image transmission enables an extended operating range.
Equipped with visual and infrared cameras for superior inspections.
Supports fully automated and precise inspection routes, allowing the drone to capture data along the designated path.
Drone Platform
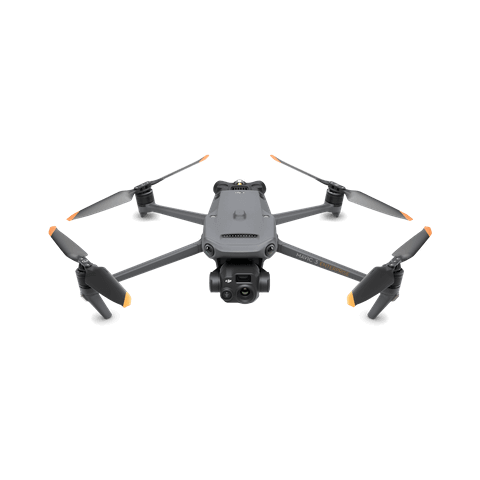
DJI Mavic 3T
... Open
Weight: 920 g
Max Flight Time (no wind): 45 mins
Sensing type: Omnidirectional binocular vision system, supplemented with an infrared sensor at the bottom of the aircraft
Environment Adaptability: Max Take-off Altitude Above Sea Level 6000m; Max Wind Speed Resistance 12 m/s
Wide Camera: 1/2-inch CMOS, Effective pixels: 48 MP
Tele Camera: 1/2-inch CMOS, Effective pixels: 12 MP
Thermal Camera: Video Resolution 640×512@30Hz
Compatible with RTK module and DJI Cellular module
Max Flight Time (no wind): 45 mins
Sensing type: Omnidirectional binocular vision system, supplemented with an infrared sensor at the bottom of the aircraft
Environment Adaptability: Max Take-off Altitude Above Sea Level 6000m; Max Wind Speed Resistance 12 m/s
Wide Camera: 1/2-inch CMOS, Effective pixels: 48 MP
Tele Camera: 1/2-inch CMOS, Effective pixels: 12 MP
Thermal Camera: Video Resolution 640×512@30Hz
Compatible with RTK module and DJI Cellular module
Payload And Software
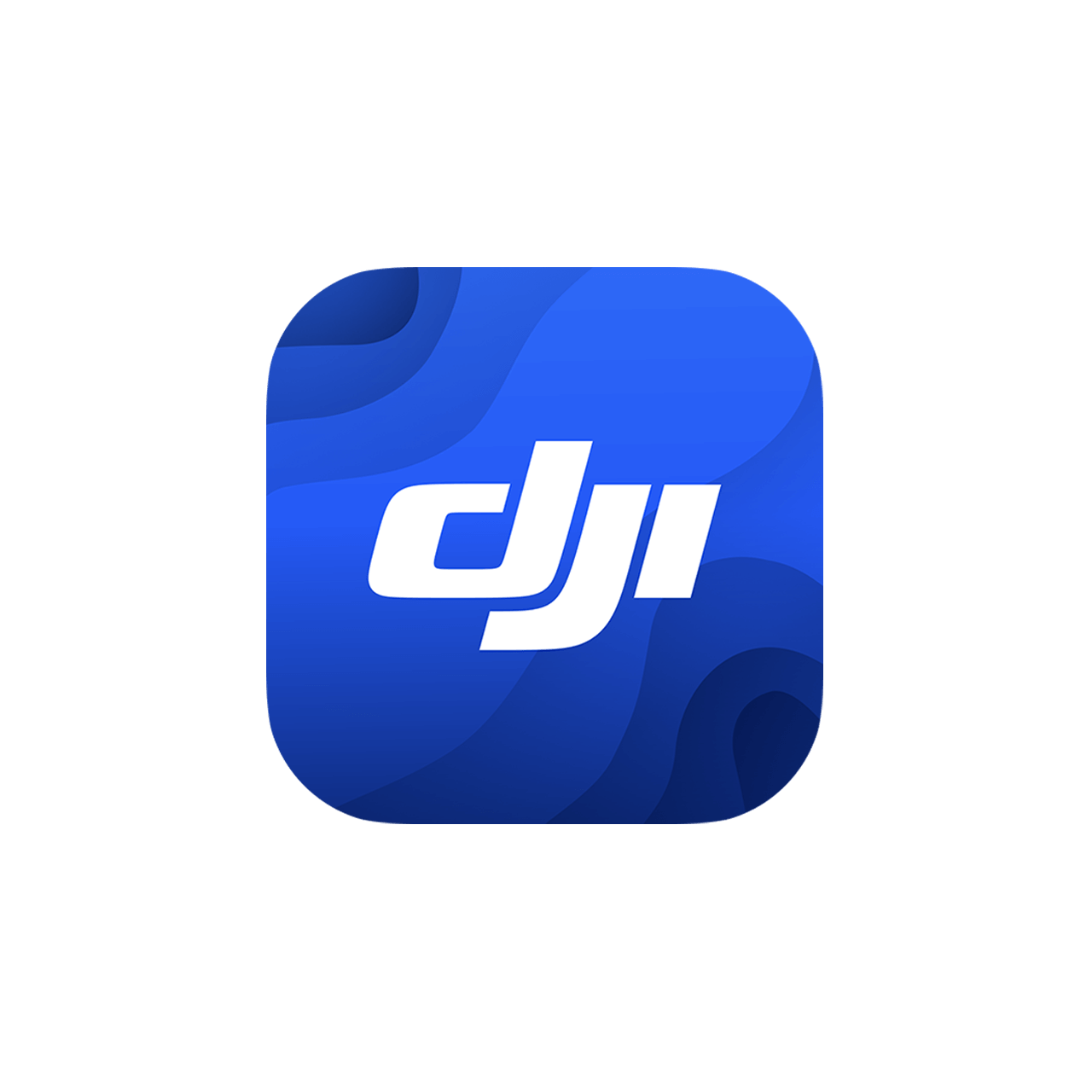
DJI Pilot 2
... Open
Ground control
Workflow
- Mission Planning:
- Plan inspection route by using Waypoint Mission or manually fly the inspection route while using the Live Mission Recording feature for future replicable missions. - Data Collection:
- Upon arrival at the takeoff point, quickly deploy the drone and initiate the previously saved inspection. The drone will automatically follow the flight route.
- During the flight, you can detect a risk situation in real time and stop the route for verification. - Data Analysis:
- After the aircraft automatically lands, export the photos taken for further analysis and identification.
Reliable Performance Inspection
The DJI Matrice 30 Series delivers portable yet powerful performance with an extended flight range of up to 15 km and ingress protection to withstand harsh weather conditions. This solution enables inspection professionals to detect abnormalities using the high-resolution visual and thermal (M30T) sensors, dual-control operations, and precise re-shooting.
This solution is compatible with the DJI Cellular module[1] for 4G-enhanced image transmission, thereby extending its effective operating range in complex urban or mountainous terrains.
This solution is compatible with the DJI Cellular module[1] for 4G-enhanced image transmission, thereby extending its effective operating range in complex urban or mountainous terrains.
The drone is foldable, portable, and can be easily transported.
Quick deployment, ready in just 2 minutes.
A laser rangefinder allows for precise defect pinpointing on the pipeline and acquisition of coordinates for targeted repair work.
Low-light mode captures detailed images even in dimly lit environments.
Cost-effective, featuring an integrated infrared camera.
Drone Platform
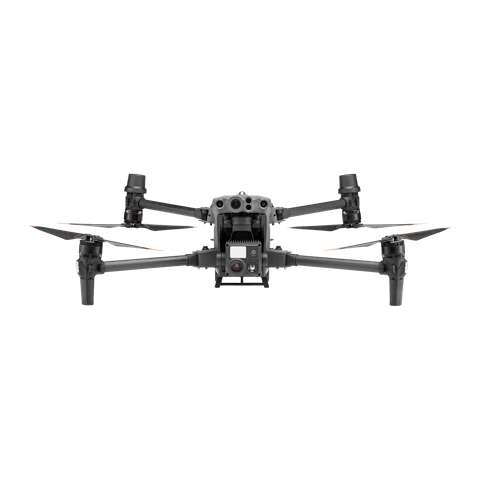
Matrice 30 Series
... Open
Weight (incl. two batteries): 3770 ± 10 g.
Max Flight Time: 41 min.
Sensing system: Six-directional sensing and positioning.
Environment Adaptability: Max Service Ceiling Above Sea Level (without other payload) 7,000 m (with 1676 propellers); Max Wind Resistance 12 m/s.
Zoom camera: 1/2-inch CMOS, Effective pixels: 48MP.
Max Flight Time: 41 min.
Sensing system: Six-directional sensing and positioning.
Environment Adaptability: Max Service Ceiling Above Sea Level (without other payload) 7,000 m (with 1676 propellers); Max Wind Resistance 12 m/s.
Zoom camera: 1/2-inch CMOS, Effective pixels: 48MP.
Payload And Software
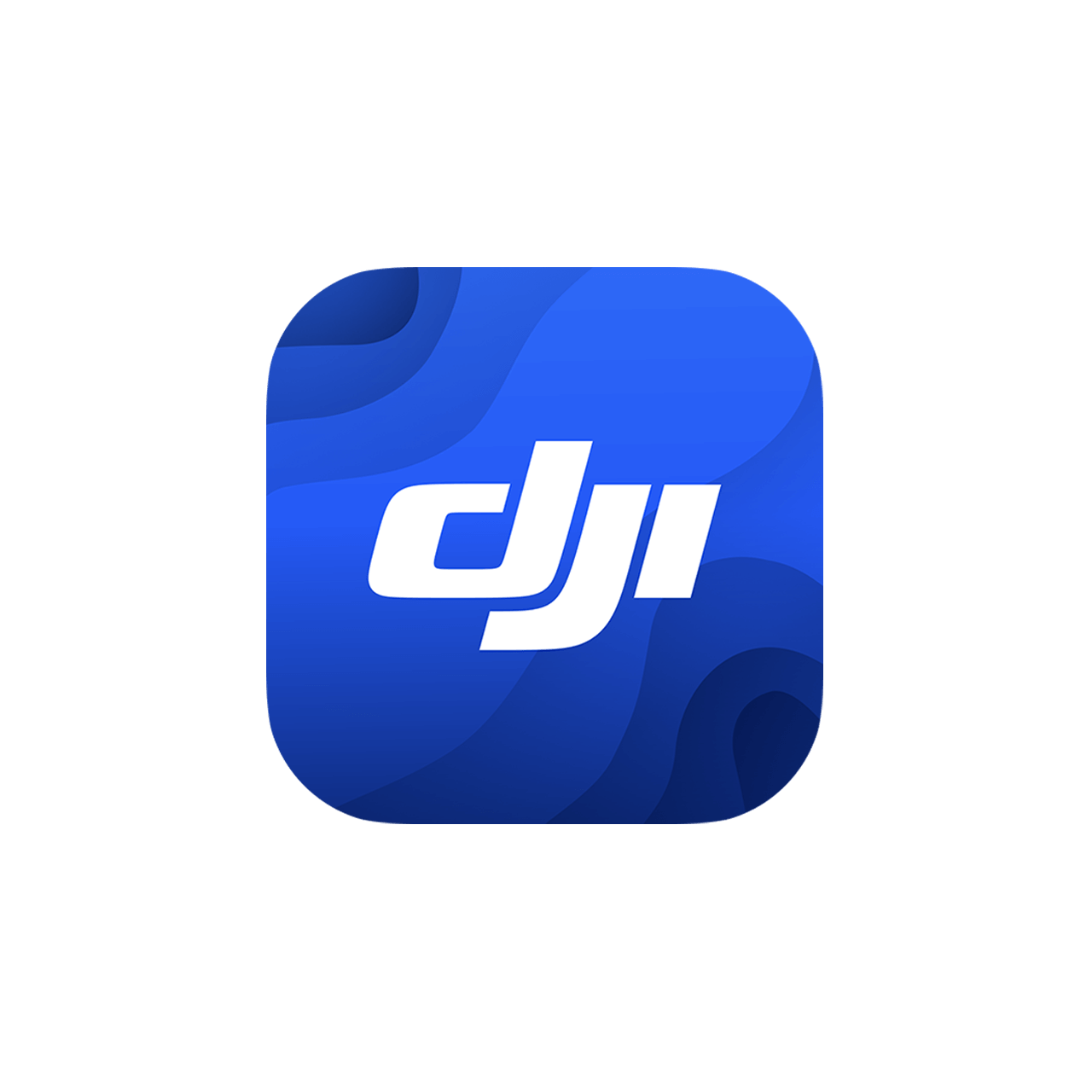
DJI Pilot 2
... Open
Ground control
Workflow
- Mission Planning:
- Plan inspection route by using Waypoint Mission or manually fly the inspection route while using the Live Mission Recording feature for future replicable missions. - Data Collection:
- Upon arrival at the takeoff point, quickly deploy the drone and initiate the previously saved inspection mission. The drone will automatically follow the flight route.
- During the flight, you can detect a risk situation in real time, stop the route for verification and pinpoint the location for further repair work. - Data Analysis:
- Analyze the images to detect defects or required maintenance work by manually reviewing the data collected. Transfer the data to a third-party software to identify equipment defects using model detection.
Leak Detection Inspection
The DJI Matrice 350 RTK is a dependable platform with interchangeable payloads tailored to meet the needs of specific tasks. Whether for mapping or inspection, the Matrice 350 RTK delivers comprehensive operational capabilities for facility managers. When paired with a third-party gas detector sensor, inspection teams can identify gas leaks that may otherwise be undetectable to the human eye.
This solution is compatible with the DJI Cellular module[1] for 4G-enhanced image transmission, thereby extending its effective operating range in complex urban or mountainous terrains.
This solution is compatible with the DJI Cellular module[1] for 4G-enhanced image transmission, thereby extending its effective operating range in complex urban or mountainous terrains.
Equipped with a variety of payloads, it provides operational efficiency and improved inspection capabilities.
Detect and accurately pinpoint leaks in real-time from a safe distance.
Longer flight times and extended transmission range allow for covering large areas.
When paired with the Zenmuse H30 Series, it offers high-definition zoom capabilities, thermal (H30T) and a laser rangefinder.
Drone Platform
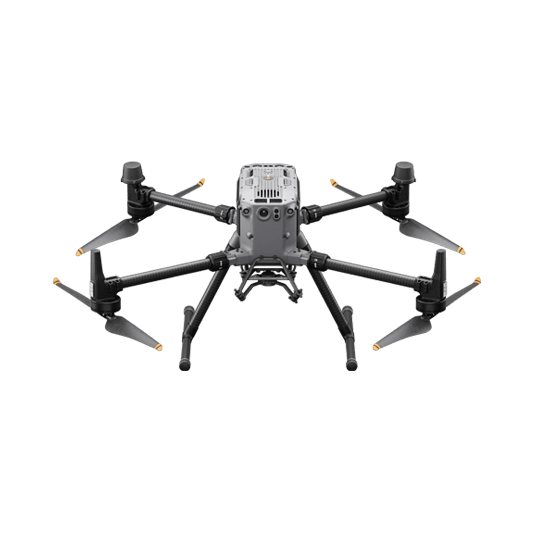
Matrice 350 RTK
... Open
Weight: Approx. 6.47 kg(with single downward gimbal and two TB65 batteries).
Max Flight Time: 55 minutes.
Sensing system: Six-directional sensing and positioning.
Environment Adaptability: IP55, Max Service Ceiling Above Sea Level 7,000 m (with 1676 propellers,without other payload); Max Wind Resistance 12 m/s.
Max Flight Time: 55 minutes.
Sensing system: Six-directional sensing and positioning.
Environment Adaptability: IP55, Max Service Ceiling Above Sea Level 7,000 m (with 1676 propellers,without other payload); Max Wind Resistance 12 m/s.
Payload And Software
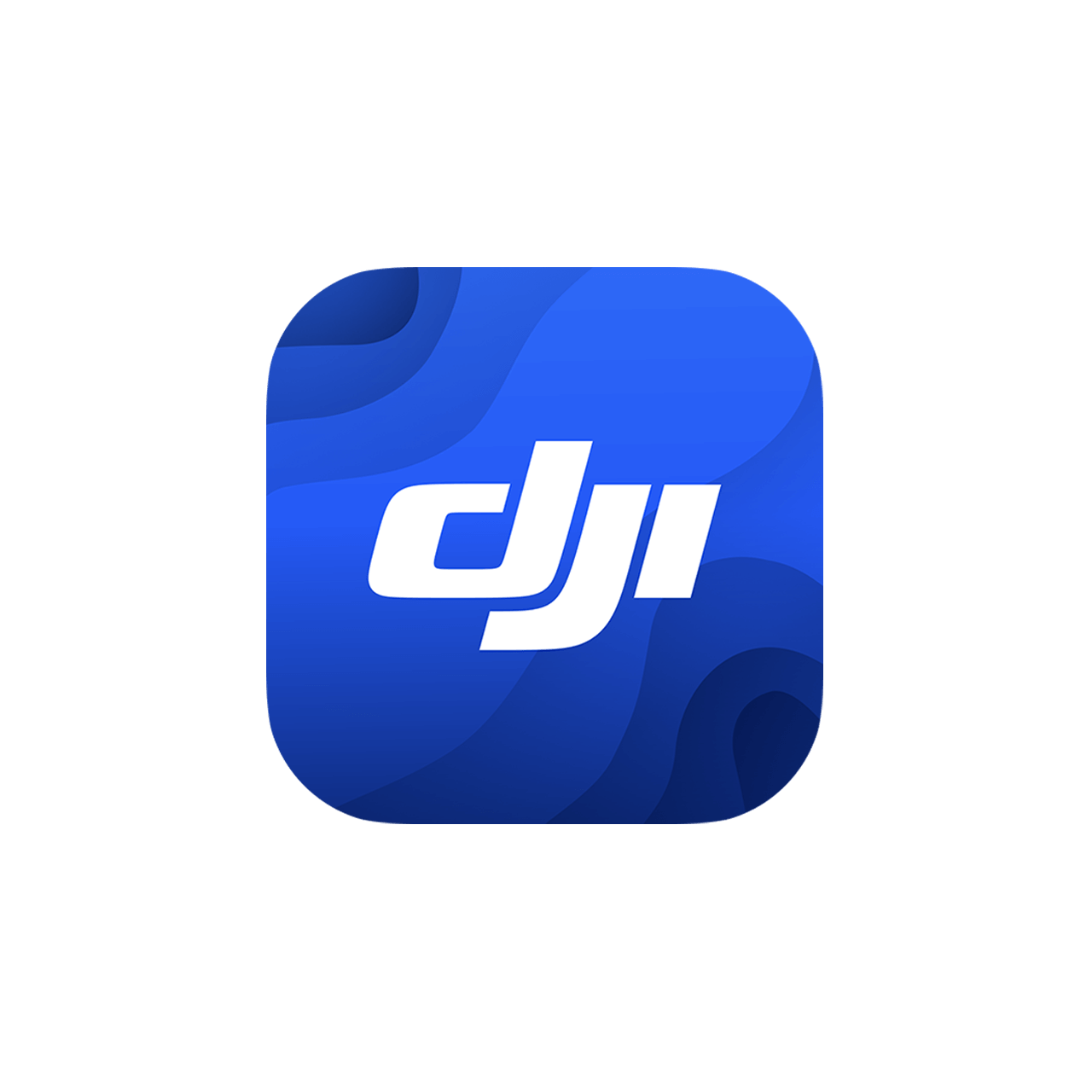
DJI Pilot 2
... Open
Ground control
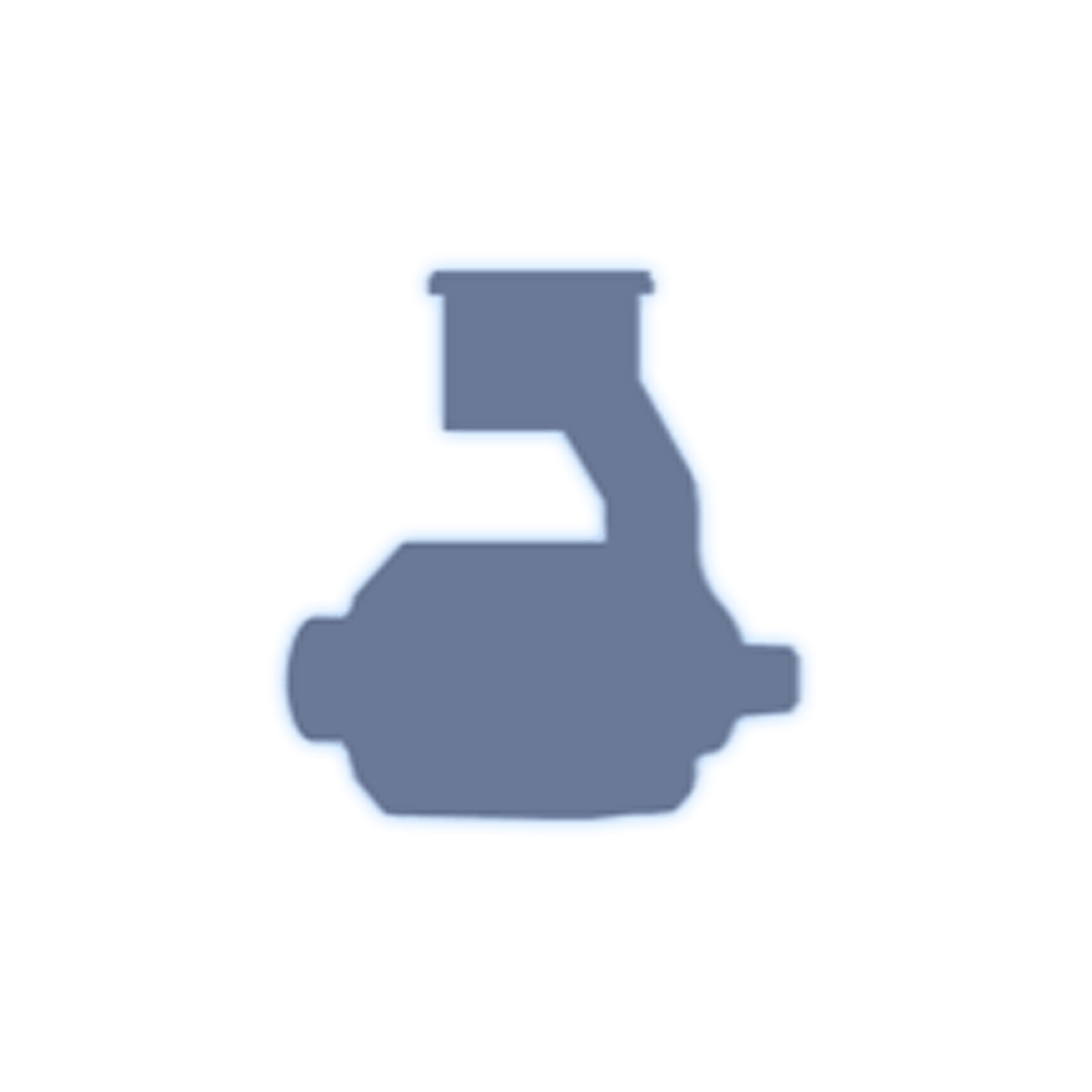
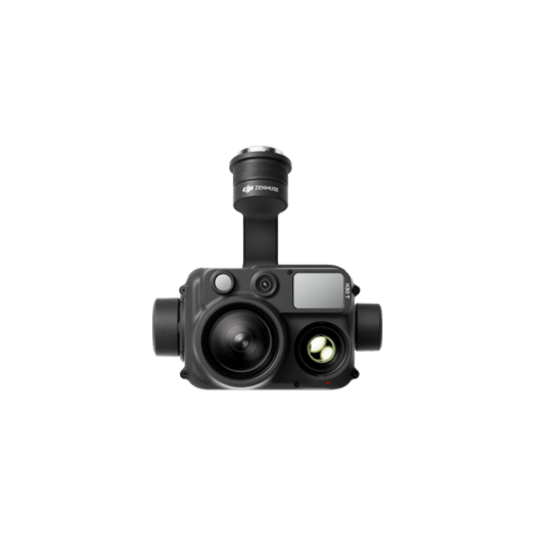
Zenmuse H30T
... Open
Weight: 920±5 g.
Ingress Protection Rating: IP54.
Zoom Camera: 1/1.8-inch CMOS, Effective Pixels: 40 MP.
Wide-Angle Camera: 1/1.3-inch CMOS, Effective Pixels: 48 MP.
Infrared Thermal Camera: 1280×1024@30fps.
Laser Range Finder: max range 3000 m.
Ingress Protection Rating: IP54.
Zoom Camera: 1/1.8-inch CMOS, Effective Pixels: 40 MP.
Wide-Angle Camera: 1/1.3-inch CMOS, Effective Pixels: 48 MP.
Infrared Thermal Camera: 1280×1024@30fps.
Laser Range Finder: max range 3000 m.
Workflow
- Data Collection:
- Fly the drone manually using the DJI Pilot 2 app or the third-party payload software.
- If the gas detector senses a leak it will trigger an alert. Capture images and sensor data on the spot to evaluate the situation. - Data Analysis:
- Review the gas sensor and visual inspection data to detect defects or required maintenance work.
Automated Routine Inspection
DJI Dock 2 (including the DJI Matrice 3D Series) integrates with DJI FlightHub 2 to enable remote, repeatable inspections, enhancing efficiency and ensuring personnel safety. Schedule automated visual or thermal inspections, and ensure inspection quality with live streams via DJI FlightHub 2.
This solution is compatible with the DJI Cellular module[1] for 4G-enhanced image transmission, extending its effective operating range in complex urban or mountainous environments.
This solution is compatible with the DJI Cellular module[1] for 4G-enhanced image transmission, extending its effective operating range in complex urban or mountainous environments.
Remote operations reduce transportation times for pilots, improving operational costs and personnel management.
Real-time live data streams provide visual and thermal information on critical equipment.
Operates in all weather conditions, day or night, adapting to various operational scenarios.
Centralized data management and analysis through DJI FlightHub 2.
Drone Platform
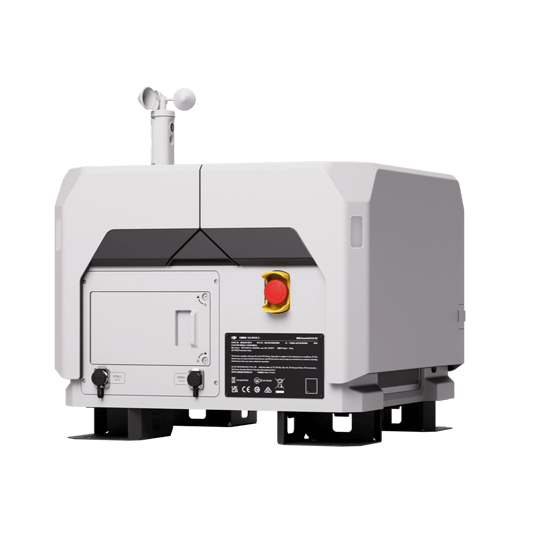
DJI Dock 2
... Open
Weight: 34 kg (without the drone).
Size: length 570 mm, width 583 mm, height 465 mm.
Environment adaptability: -25℃-45℃ working temperature, IP55 Rate, max operation height 4,000 m.
Max Operating Radius: 10 km.
Size: length 570 mm, width 583 mm, height 465 mm.
Environment adaptability: -25℃-45℃ working temperature, IP55 Rate, max operation height 4,000 m.
Max Operating Radius: 10 km.
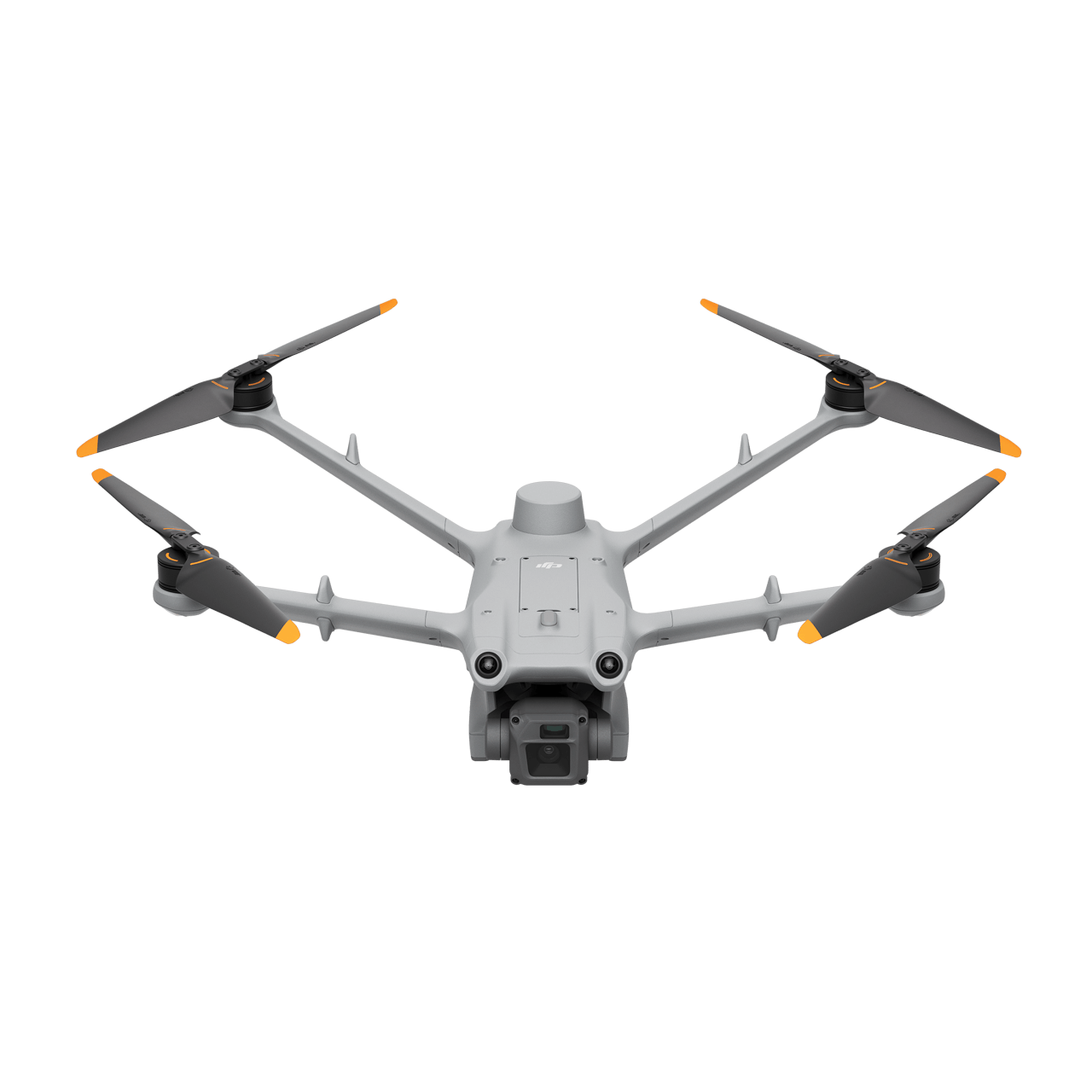
Matrice 3D
... Open
Weigh: 1410 g.
Size: length 335 mm, width 398 mm, height 153 mm(without propellers).
Max flight time: 50 minutes.
Max Operating Radius: 10 km.
Wide camera: 4/3 CMOS, 20MP, Mechanical Shutter: 8-1/2000 s.
Tele camera: 1/2" CMOS, 12MP.
Environment adaptability: -25℃-45℃ working temperature, IP55 Rate, max operation height 4,000m.
Size: length 335 mm, width 398 mm, height 153 mm(without propellers).
Max flight time: 50 minutes.
Max Operating Radius: 10 km.
Wide camera: 4/3 CMOS, 20MP, Mechanical Shutter: 8-1/2000 s.
Tele camera: 1/2" CMOS, 12MP.
Environment adaptability: -25℃-45℃ working temperature, IP55 Rate, max operation height 4,000m.
Payload And Software
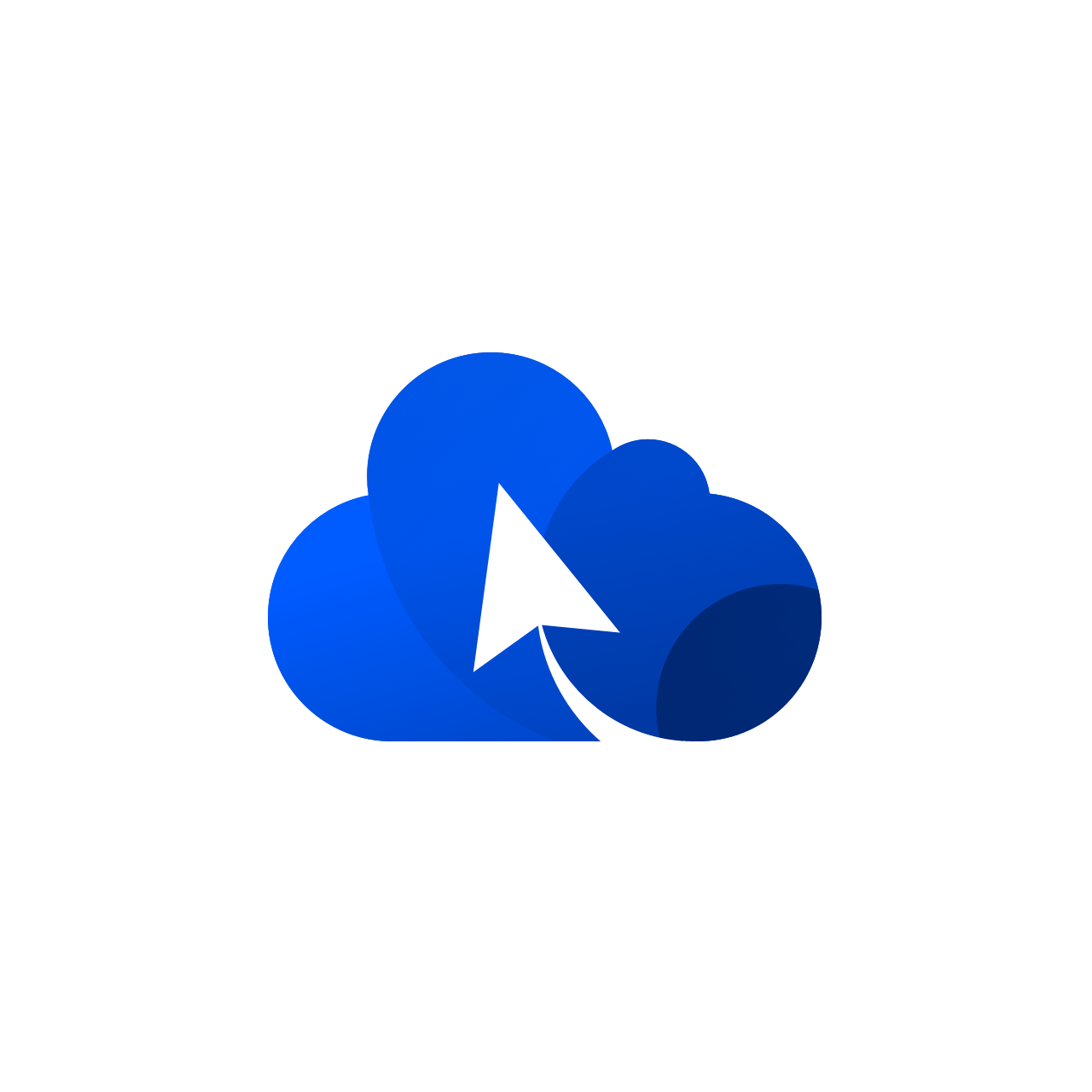
Workflow
- Mission Planning:
- Use DJI FlightHub 2 or preferred third-party sofware to plan inspection routes based on pipeline models and maps.
- Or import previously saved inspection flight routes to the DJI FlightHub 2 via the Pilot 2 app using the Live Mission Recording feature. - Data Collection:
- Using DJI FlightHub 2, select the preferred dock and scheduled inspection mission.
- The DJI Matrice 3D or Matrice 3TD will execute inspection tasks as planned, and the captured results will be automatically uploaded to the DJI FlightHub 2 cloud platform. - Data Analysis:
- Analyze the inspection photos manually or export to a third-party model detection software to identify defects or deterioration on the components.
1. This service is not available in some countries and regions. Please consult your local dealer for details.