Bridge Inspection
Drones equipped with high-resolution cameras can meticulously inspect critical bridge components, including decks, piers, and cables. Utilizing LiDAR technology, they can swiftly generate BIM and digital twin models, facilitating faster and more cost-effective assessments. This technological approach aids builders, maintainers, and auditors in comprehending the bridge's condition and in planning maintenance in a proactive manner.
Painpoints
Advantages
Traditional bridge inspections often necessitate workers climbing the structures or utilizing aerial work platforms, presenting significant safety hazards, particularly under adverse weather conditions.
Enable the inspection of hard-to-reach areas, such as high altitudes or confined spaces, without endangering inspection personnel.
Manual inspections can be time-intensive, especially for expansive bridges, leading not only to prolonged durations but also potential traffic disruptions.
Expedite the coverage of extensive bridge structures through automated mission planning or manual control, diminishing inspection durations and eliminating coverage gaps.
Bridge inspections demand considerable manpower and specialized equipment, such as aerial work platforms and hanging baskets, which escalate the costs.
Lower inspection costs and enhance inspection frequency with user-friendly and economical drone solutions.
Manual inspections might not encompass all bridge areas, particularly those that are challenging to access, potentially resulting in incomplete data and compromising the accuracy of the inspection outcomes.
Drones, outfitted with high-resolution cameras and additional sensors, can detect minute details, such as fine cracks, corrosion, and other structural issues. This data can be further analyzed using image processing software to heighten inspection precision.
The effective analysis and processing of extensive data collected remain a challenge. Conventional methods typically depend on manual recording and analysis, which are inefficient and susceptible to errors.
Produce high-quality data that can be archived and scrutinized for ongoing bridge health monitoring. By comparing data across different time points, it is feasible to detect trends in the bridge's structural integrity and preemptively alert to potential issues.
Solution
Bridge Visual Inspection
Bridge Digital Twin Asset Management
Portable Maneuverable Inspection
Bridge Visual Inspection
The Matrice 350 RTK, equipped with the Zenmuse P1, captures high-resolution images of bridge structures and key components to identify cracks or signs of deterioration. With the addition of CSM Radar, it provides a 360-degree obstacle avoidance sensor, enabling closer inspections without compromising flight safety.
The Zenmuse P1 features a full-frame sensor with interchangeable fixed-focus lenses mounted on a 3-axis stabilized gimbal for precision imaging.
Hot-swappable batteries ensure minimal downtime during operations.
Capable of carrying various payloads, the drone offers enhanced inspection capabilities.
Extended flight time allows for longer single-operation periods.
Dual-control operations increase reliability and enhance operational safety.
Drone Platform
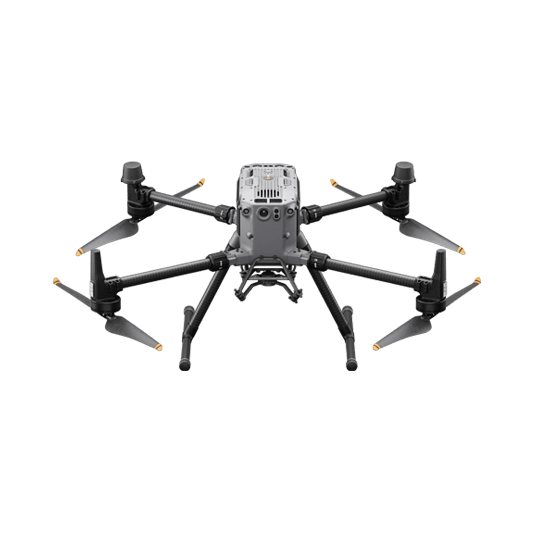
Matrice 350 RTK
... Open
Weight: Approx. 6.47 kg(with single downward gimbal and two TB65 batteries).
Max Flight Time: 55 minutes.
Sensing system: Six-directional sensing and positioning.
Environment Adaptability: IP55, Max Service Ceiling Above Sea Level 7,000 m (with 1676 propellers,without other payload); Max Wind Resistance 12 m/s.
Max Flight Time: 55 minutes.
Sensing system: Six-directional sensing and positioning.
Environment Adaptability: IP55, Max Service Ceiling Above Sea Level 7,000 m (with 1676 propellers,without other payload); Max Wind Resistance 12 m/s.
Payload And Software
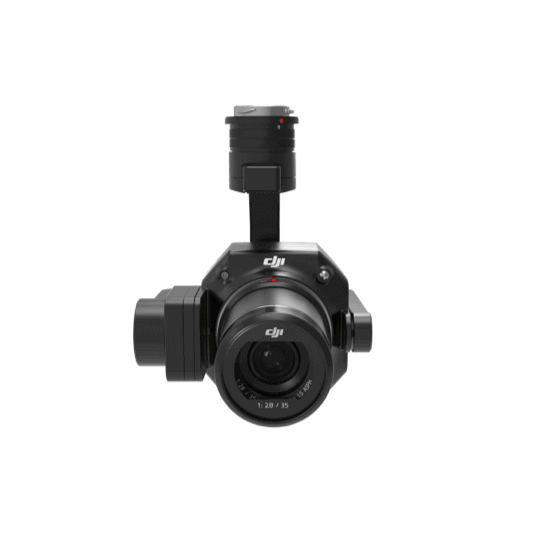
Zenmuse P1
... Open
45 MP Full-frame camera.
Global Mechanical Shutter Shutter Speed 1/2000 Seconds.
3-axis Stabilized Gimbal Smart Oblique Capture.
Global Mechanical Shutter Shutter Speed 1/2000 Seconds.
3-axis Stabilized Gimbal Smart Oblique Capture.
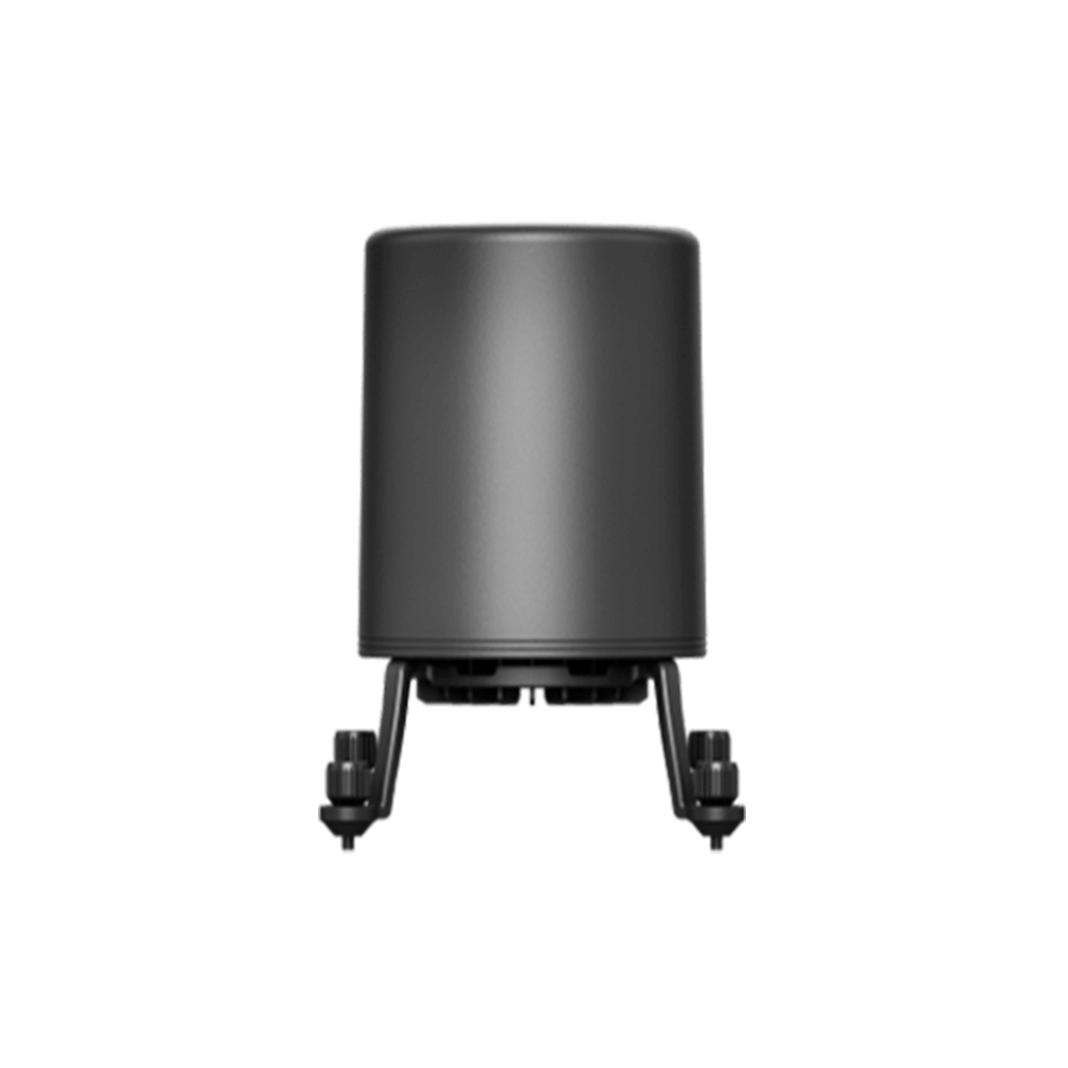
CSM Radar
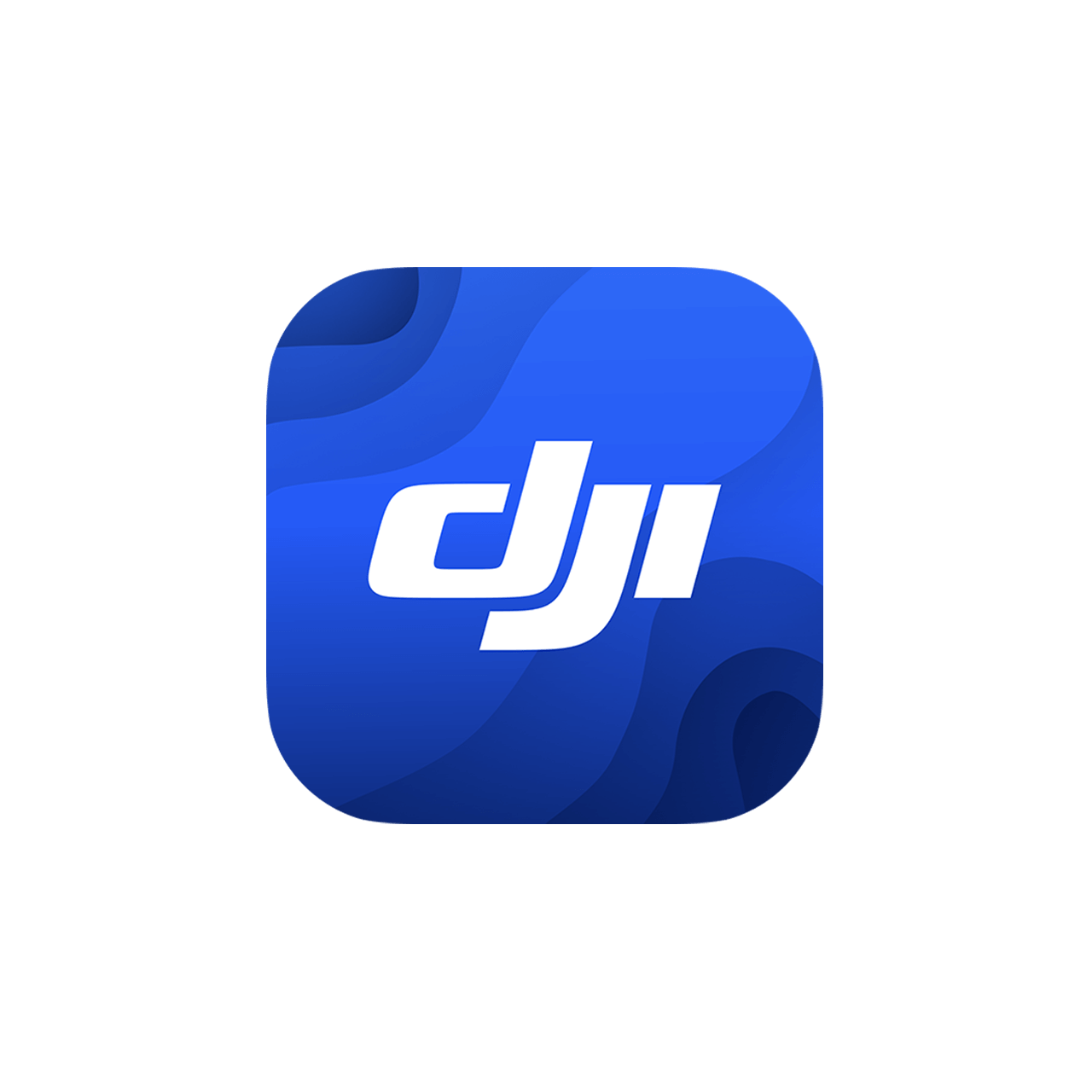
DJI Pilot 2
... Open
Ground control
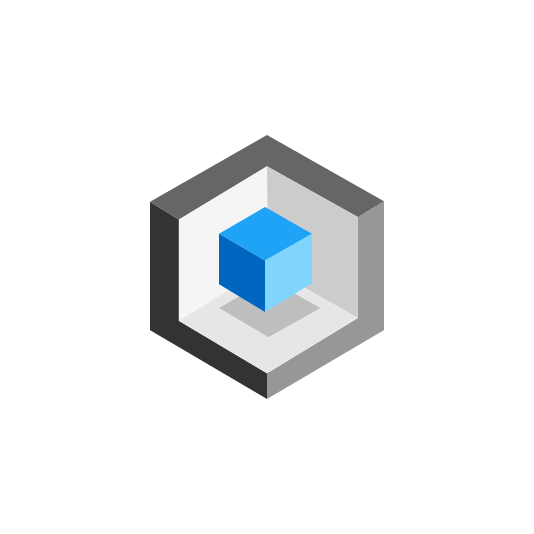
Workflow
- Mission Planning:
- Using third-party software, plan an inspection waypoint route based on bridge 3D models or use live mission recording with AI spot checking in the DJI Pilot 2 to create a routine inspection route. - Data Collection:
- Import the flight route into Pilot 2 and execute the mission. Turn on the RTK for better results. - Data Processing:
- Reconstruct vertical 2D models through DJI Terra. Improve model texture by editing it using DJI Modify. - Data Analysis:
- Analyze the inspection photos or detail modes to identify and locate any defects. Document the required maintenance using the images or model findings.
Bridge Digital Twin Asset Management
The Matrice 350 RTK, when equipped with the Zenmuse P1, can generate high-resolution 3D models for detailed visual inspection. With the Zenmuse L2 LiDAR attached, the Matrice 350 RTK performs laser point cloud digitization to model bridges accurately.
Utilize DJI Terra to produce both photogrammetry and point cloud models. Enhance your photogrammetry models by editing and correcting textures with DJI Modify.
Utilize DJI Terra to produce both photogrammetry and point cloud models. Enhance your photogrammetry models by editing and correcting textures with DJI Modify.
Create detailed models of complex structures by combining photogrammetry and LiDAR scanning sensors on a single drone.
Easily share models with team members using a link.
Review and identify defects in the models from an overarching perspective.
Drone Platform
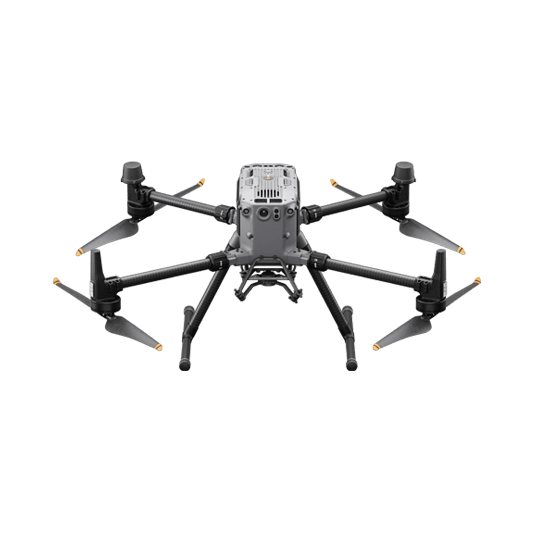
Matrice 350 RTK
... Open
Weight: Approx. 6.47 kg(with single downward gimbal and two TB65 batteries).
Max Flight Time: 55 minutes.
Sensing system: Six-directional sensing and positioning.
Environment Adaptability: IP55, Max Service Ceiling Above Sea Level 7,000 m (with 1676 propellers,without other payload); Max Wind Resistance 12 m/s.
Max Flight Time: 55 minutes.
Sensing system: Six-directional sensing and positioning.
Environment Adaptability: IP55, Max Service Ceiling Above Sea Level 7,000 m (with 1676 propellers,without other payload); Max Wind Resistance 12 m/s.
Payload And Software
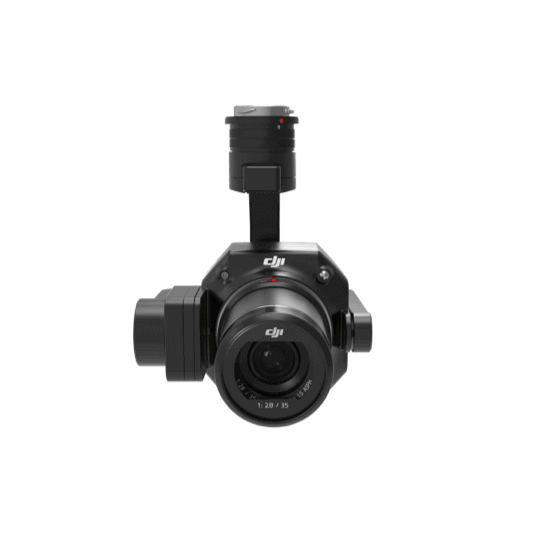
Zenmuse P1
... Open
45 MP Full-frame camera.
Global Mechanical Shutter Shutter Speed 1/2000 Seconds.
3-axis Stabilized Gimbal Smart Oblique Capture.
Global Mechanical Shutter Shutter Speed 1/2000 Seconds.
3-axis Stabilized Gimbal Smart Oblique Capture.
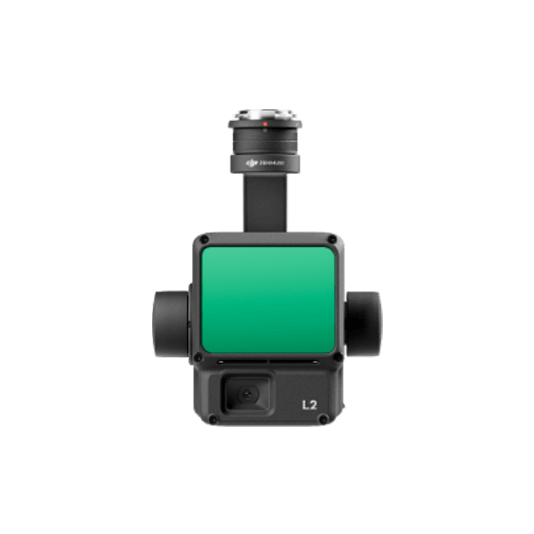
Zenmuse L2
... Open
Integrates frame LiDAR, a self-developed high-accuracy IMU system, and a 4/3 CMOS RGB mapping camera.
2.5 km2 covered in a single flight.
Detection Range 250m @10% reflectivity, 100klx.
Effective Point Cloud Rate: 240,000 pts/s.
Supports 5 Returns.
Turnkey Solution.
2.5 km2 covered in a single flight.
Detection Range 250m @10% reflectivity, 100klx.
Effective Point Cloud Rate: 240,000 pts/s.
Supports 5 Returns.
Turnkey Solution.
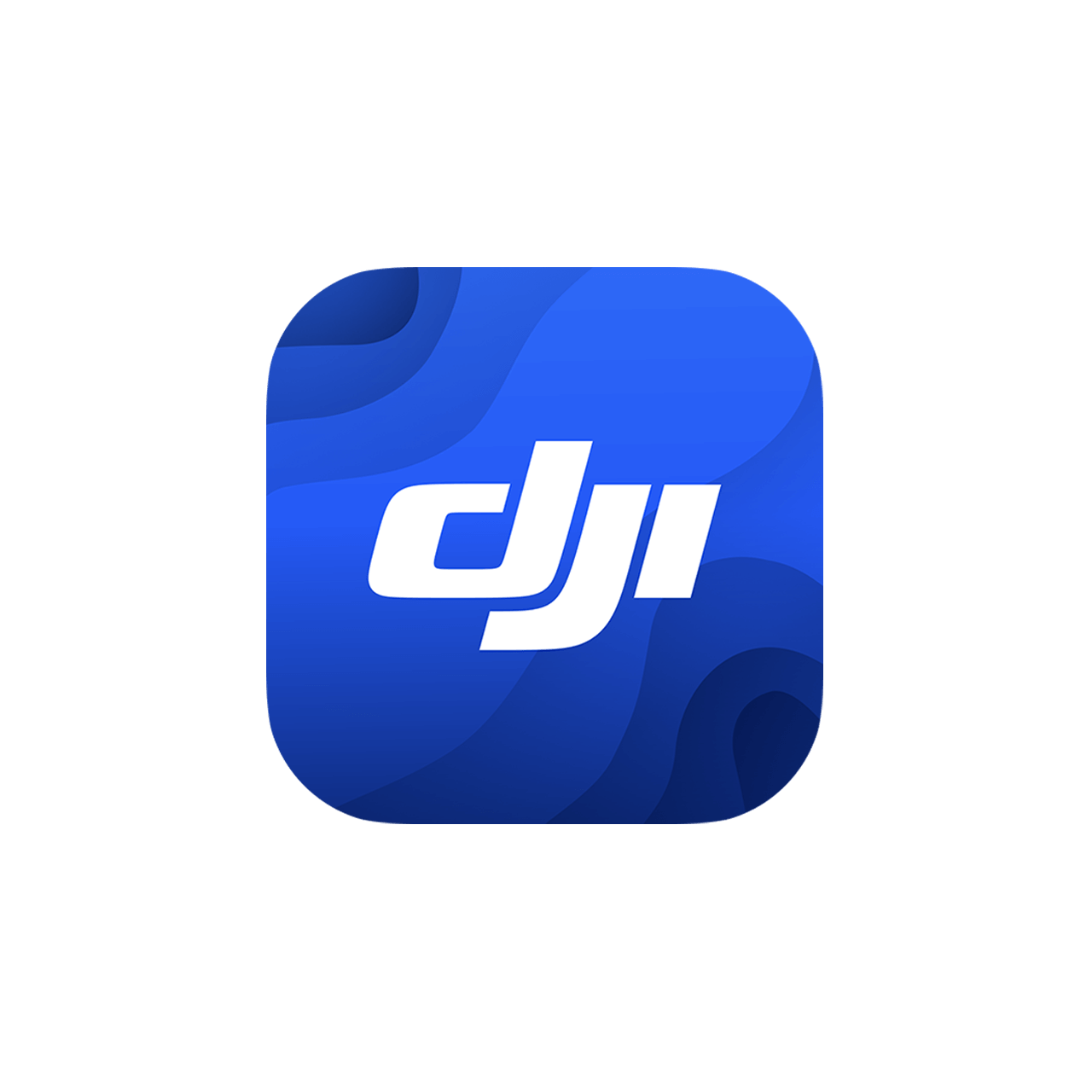
DJI Pilot 2
... Open
Ground control
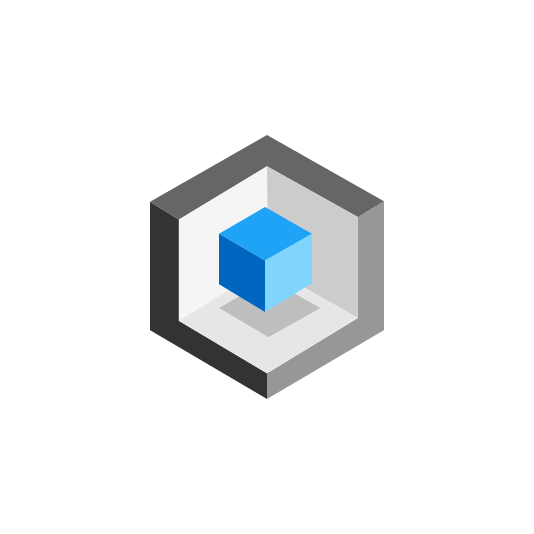
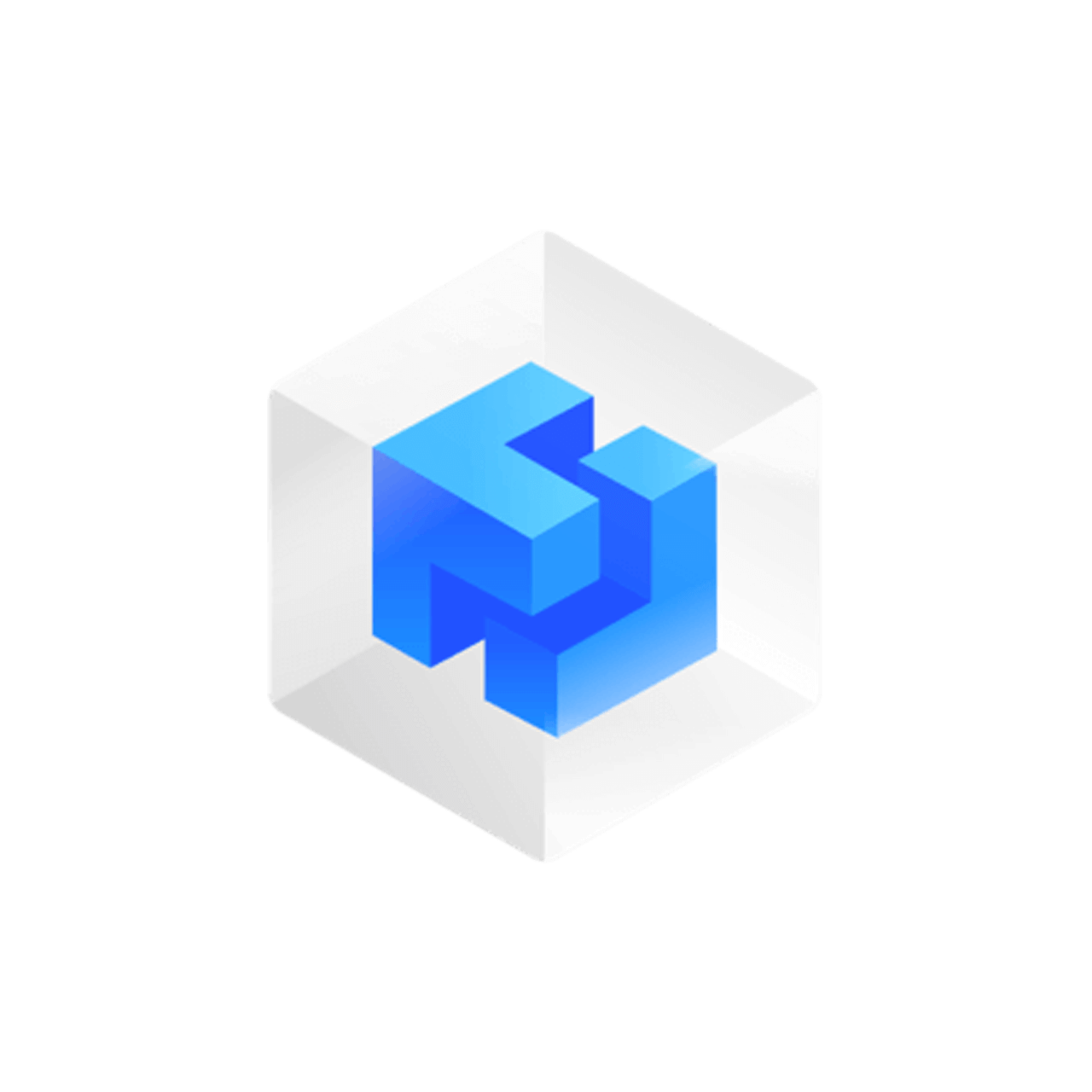
Workflow
- Data Collection:
- Using the DJI Pilot 2 app and the 3D Mapping Flight Mission feature, captured the data with the Zenmue L2 to generate a 3D point cloud model of the bridge or generate a photogrammetry 3D model using the Zenmuse P1. - Data Processing:
- Input the data to DJI Terra, then reconstuct a high resolution 3D model.
- Use DJI modify to remove the floating, black hole, which will improve model appereance. - Data Analysis:
- Share the models as digital twin BIM to get the overview enviroment and set up suitable maintanence plan.
Portable Maneuverable Inspection
The DJI Mavic 3E drones are compact and adept at navigating through the relatively narrow spaces found within complex structures. They are equipped with high-definition visible light cameras that can generate accurate 3D models and conduct detailed inspections of bridges, thereby reducing risks and manual labor.
The compact size of the drone facilitates navigation through confined spaces while adhering to safety regulations and providing optimal shooting angles.
The integration of multi-sensor technology and RTK positioning ensures high levels of positioning and modeling accuracy.
Automated flight paths, based on pre-planned routes, minimize the need for manual operation.
Drone Platform
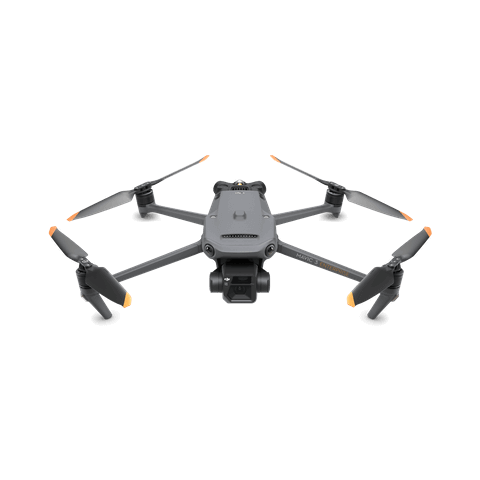
DJI Mavic 3E
... Open
Weight: 915 g.
Max Flight Time (no wind): 45 mins.
Sensing type: Omnidirectional binocular vision system, supplemented with an infrared sensor at the bottom of the aircraft.
Environment Adaptability: Max Take-off Altitude Above Sea Level 6,000 m; Max Wind Speed Resistance 12 m/s.
Wide Camera: 4/3 CMOS, Effective pixels: 20 MP.
Mechanical Shutter: 8-1/2000 s, supports rapid 0.7-second interval shooting.
Compatible with RTK module and DJI Cellular module.
Max Flight Time (no wind): 45 mins.
Sensing type: Omnidirectional binocular vision system, supplemented with an infrared sensor at the bottom of the aircraft.
Environment Adaptability: Max Take-off Altitude Above Sea Level 6,000 m; Max Wind Speed Resistance 12 m/s.
Wide Camera: 4/3 CMOS, Effective pixels: 20 MP.
Mechanical Shutter: 8-1/2000 s, supports rapid 0.7-second interval shooting.
Compatible with RTK module and DJI Cellular module.
Payload And Software
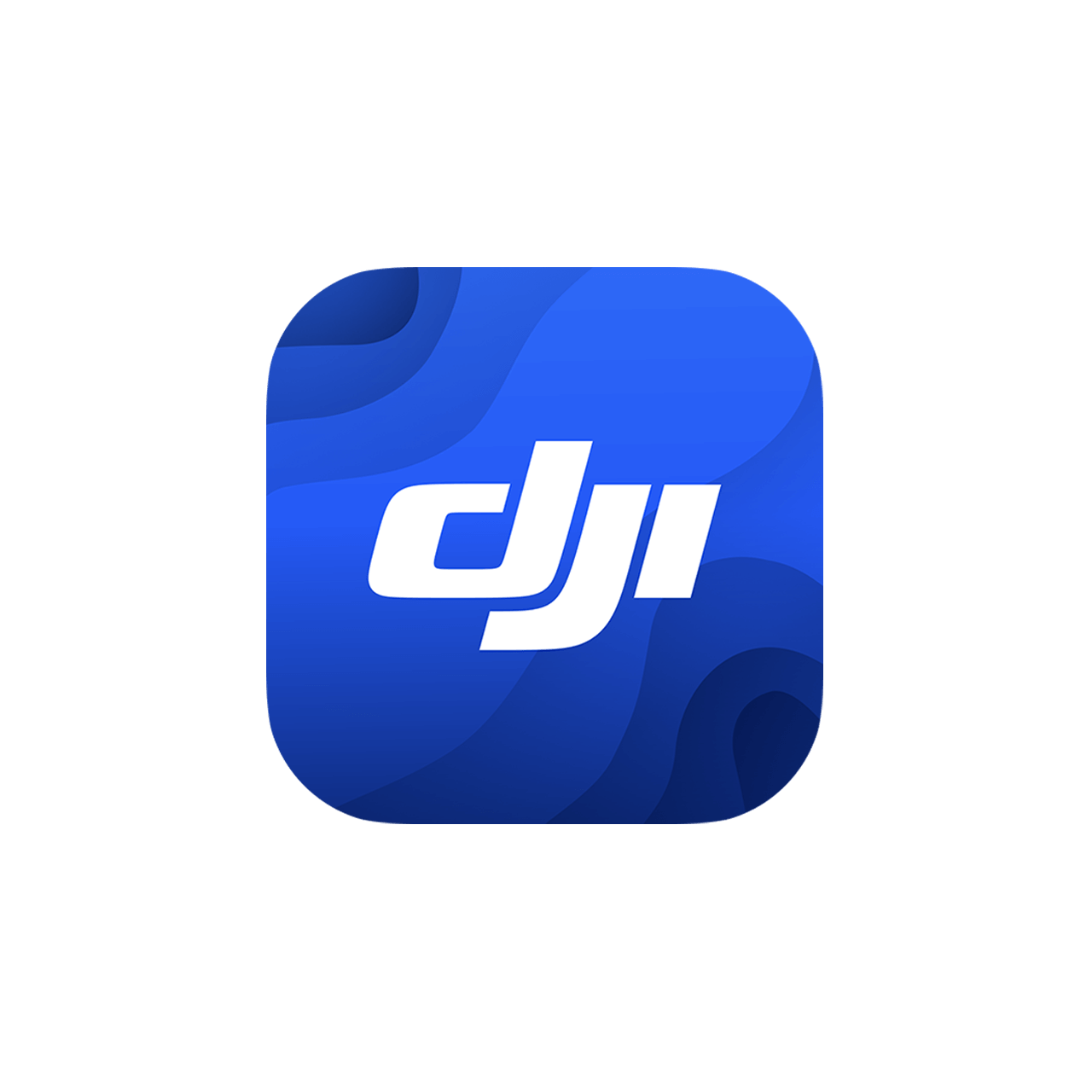
DJI Pilot 2
... Open
Ground control
Workflow
- Mission Planning:
- Using the DJI Pilot 2 app and the 3D Mapping Flight Mission feature, generate a model of the bridge to be used as a reference for detailed inspection planning.
- Use software like DJI Terra or DJI FlightHub 2 to plan inspection flight routes based on high-definition 3D models of the bridge using Slope Mission and Geometric Flight Mission. - Data Collection:
- Upload the flight path to the Mavic 3E drone. The drone automatically execute pre-planned flight route, capturing inspection photos. Complement the data collection by manually flying into hard to reach locations and capture different angles of the bridge. - Data Analysis:
- Review the images manually or import to a third-party software to identify structure defects using model detection.