Substation Inspection
Substations and converter stations serve as essential nodes within the electrical grid, and their secure and reliable functioning depends on thorough and systematic inspections. Drones offer the agility and versatility to create precise digital replicas of these substations and conduct detailed examinations of electrical components using both visible and infrared imaging. This allows for the early detection of faults, thereby reinforcing the continuous and stable operation of the substations.
Painpoints
Advantages
Manual inspections are labor-intensive and involve navigating complex structures, with evaluations largely based on the subjective assessments of inspectors.
Automated inspection protocols reduce the necessity for hands-on involvement and decrease the duration spent on-site, thereby enhancing efficiency and quality.
High-voltage equipment necessitates strict adherence to safety clearances, which restricts the accessibility of inspection personnel to certain zones and apparatuses.
Drones are capable of approaching electrical equipment closely or utilizing high-resolution zoom lenses to obtain sharp, intricate visuals.
The inspection of vital components such as transformers, circuit breakers, and busbars is often hindered by limited visibility, complicating the task of achieving a comprehensive inspection and posing difficulties in the efficient management of inspection data.
Aerial inspections offer novel vantage points for inspecting critical components and facilitate the assessment of equipment condition through advanced thermal imaging analysis.
Solution
Portable Inspection
Automated Remote Inspection
Multipurpose Drone Inspection
Portable Inspection
The DJI Mavic 3E / 3T drones are compact and capable of navigating through the relatively narrow spaces between equipment. They are equipped with high-definition visible light and infrared cameras (M3T) that can generate accurate 3D models and conduct detailed inspections of power equipment, thereby reducing risks and manual labor.
The compact size enables navigation through the confined spaces of substations while adhering to safety regulations, providing optimal shooting angles.
Integration of multi-sensor technology and RTK positioning ensures robust resistance to electromagnetic interference.
Automated flight along a pre-planned route minimizes the need for manual control.
Drone Platform
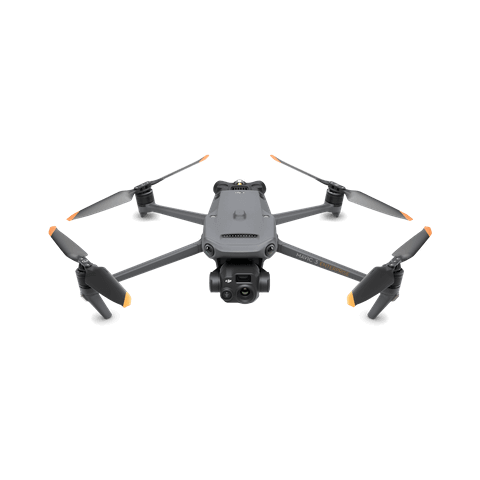
DJI Mavic 3T
... Open
Weight: 920 g
Max Flight Time (no wind): 45 mins
Sensing type: Omnidirectional binocular vision system, supplemented with an infrared sensor at the bottom of the aircraft
Environment Adaptability: Max Take-off Altitude Above Sea Level 6000m; Max Wind Speed Resistance 12 m/s
Wide Camera: 1/2-inch CMOS, Effective pixels: 48 MP
Tele Camera: 1/2-inch CMOS, Effective pixels: 12 MP
Thermal Camera: Video Resolution 640×512@30Hz
Compatible with RTK module and DJI Cellular module
Max Flight Time (no wind): 45 mins
Sensing type: Omnidirectional binocular vision system, supplemented with an infrared sensor at the bottom of the aircraft
Environment Adaptability: Max Take-off Altitude Above Sea Level 6000m; Max Wind Speed Resistance 12 m/s
Wide Camera: 1/2-inch CMOS, Effective pixels: 48 MP
Tele Camera: 1/2-inch CMOS, Effective pixels: 12 MP
Thermal Camera: Video Resolution 640×512@30Hz
Compatible with RTK module and DJI Cellular module
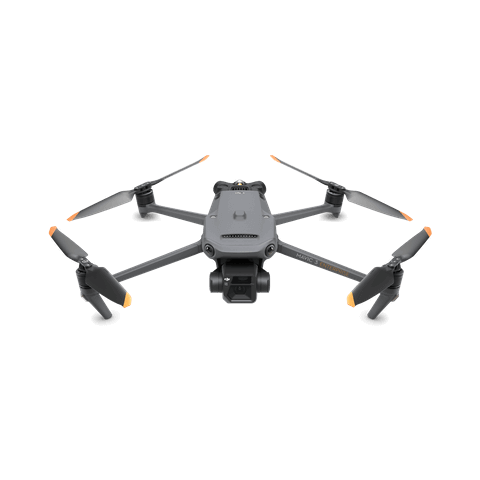
DJI Mavic 3E
... Open
Weight: 915 g.
Max Flight Time (no wind): 45 mins.
Sensing type: Omnidirectional binocular vision system, supplemented with an infrared sensor at the bottom of the aircraft.
Environment Adaptability: Max Take-off Altitude Above Sea Level 6,000 m; Max Wind Speed Resistance 12 m/s.
Wide Camera: 4/3 CMOS, Effective pixels: 20 MP.
Mechanical Shutter: 8-1/2000 s, supports rapid 0.7-second interval shooting.
Compatible with RTK module and DJI Cellular module.
Max Flight Time (no wind): 45 mins.
Sensing type: Omnidirectional binocular vision system, supplemented with an infrared sensor at the bottom of the aircraft.
Environment Adaptability: Max Take-off Altitude Above Sea Level 6,000 m; Max Wind Speed Resistance 12 m/s.
Wide Camera: 4/3 CMOS, Effective pixels: 20 MP.
Mechanical Shutter: 8-1/2000 s, supports rapid 0.7-second interval shooting.
Compatible with RTK module and DJI Cellular module.
Payload And Software
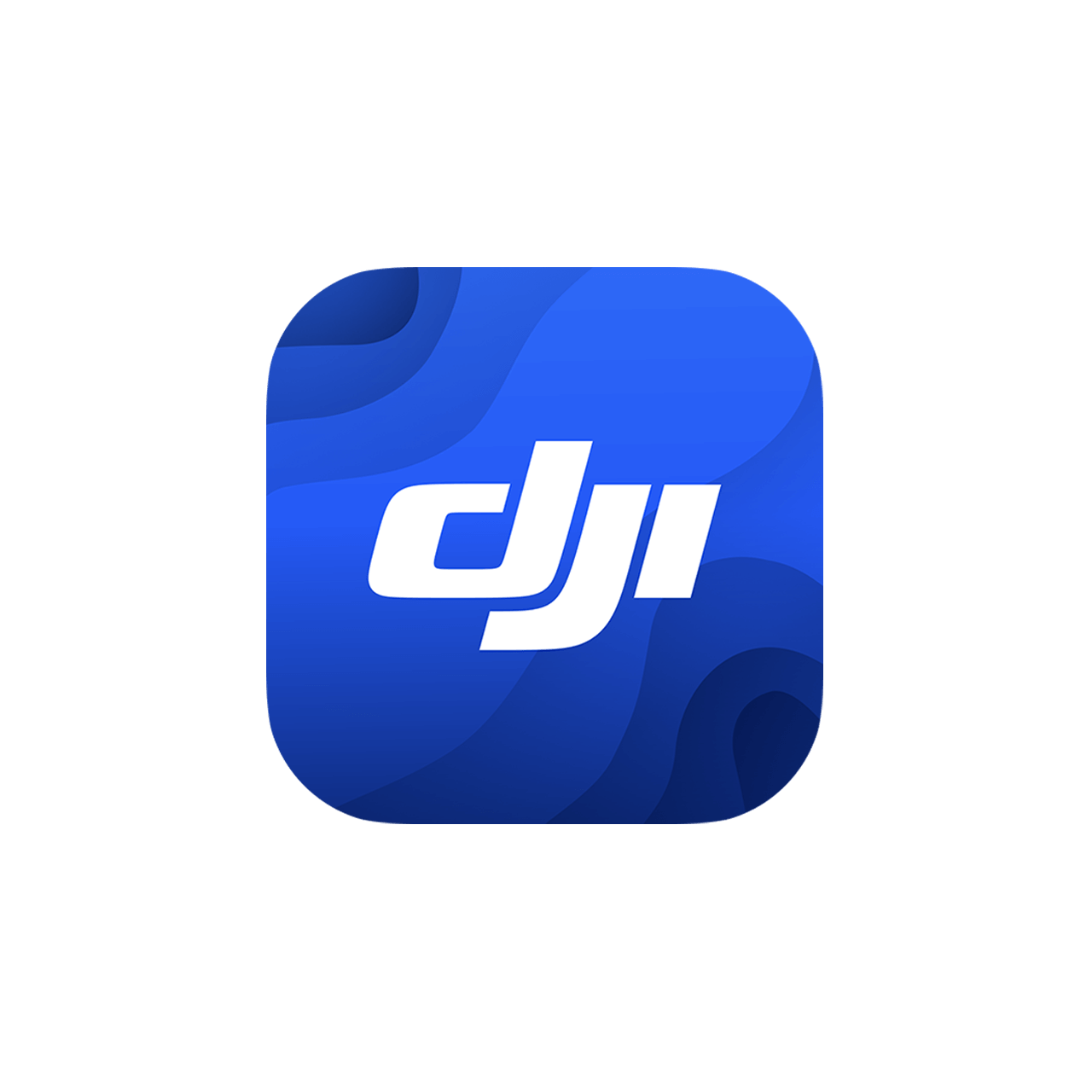
DJI Pilot 2
... Open
Ground control
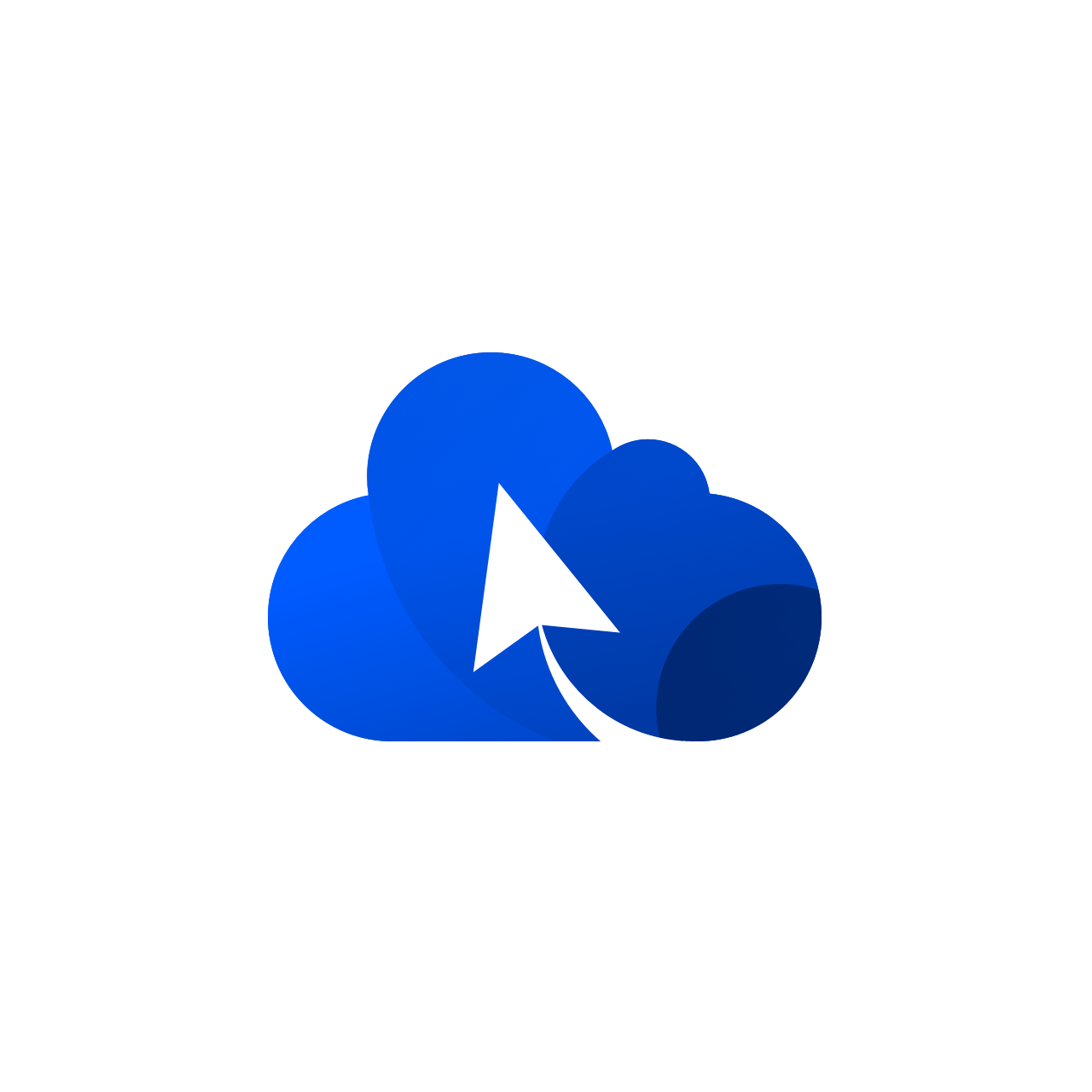
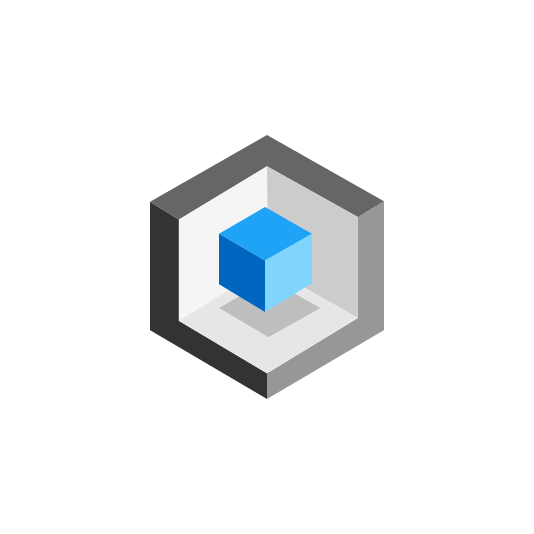
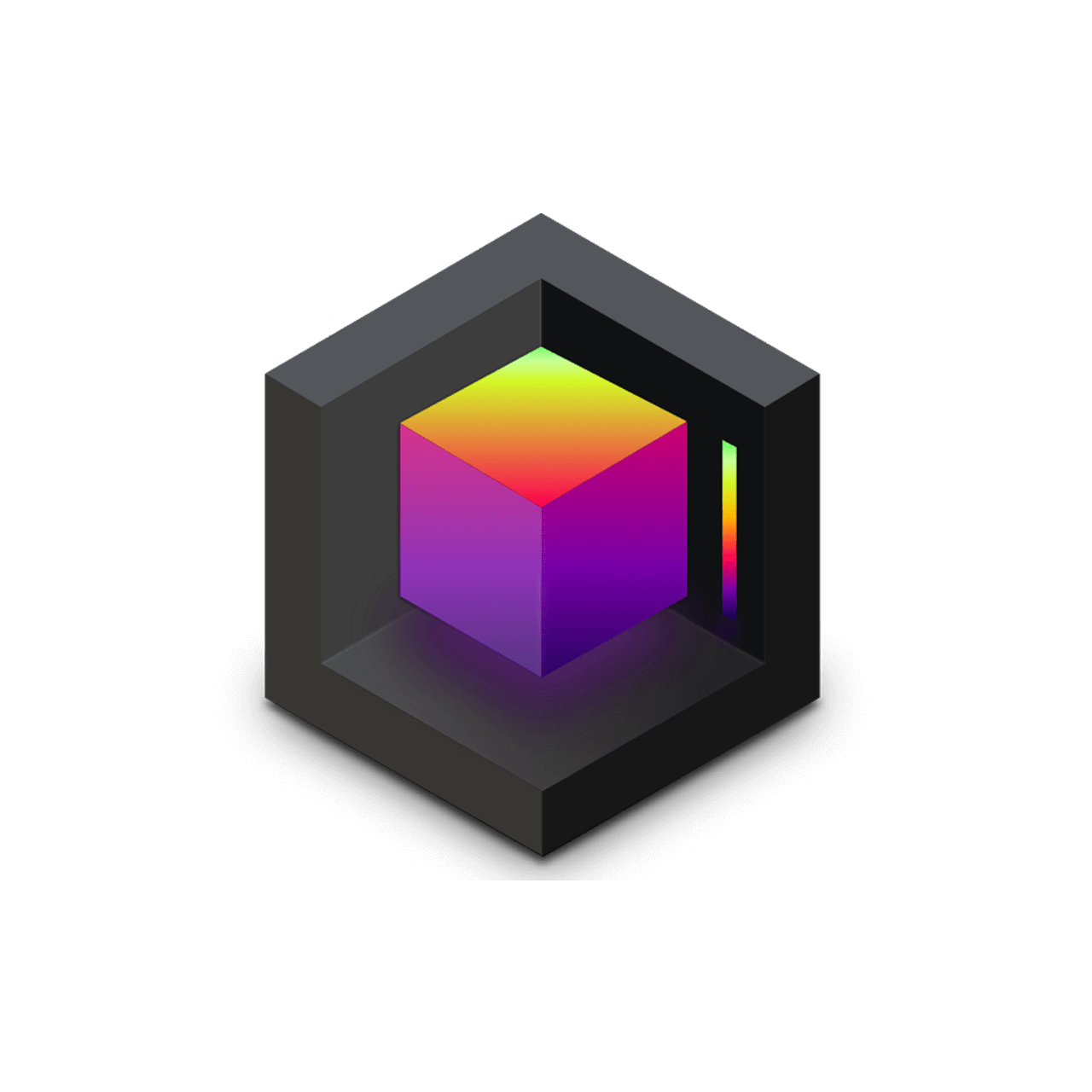
DJI Thermal Analysis Tool 3
... Open
By identifying the temperature information of critical areas of the target, the software can be used to analyze objects across many industrial applications.
Workflow
- Mission Planning:
- Use software like DJI Terra or DJI FlightHub 2 to plan inspection flight routes based on high-definition 3D models of the substation. - Data Collection:
- Upload the flight path to the Mavic 3E / 3T drone.The drone automatically execute pre-planned flight route, capturing visible light and infrared inspection photos. - Data Analysis:
- Import the images to DJI Thermal Analysis Tool to analyze the inspection results manually or with import to a third-party software to identify equipment defects using model detection.
Automated Remote Inspection
The DJI Dock 2 and the Matrice 3TD, when paired with DJI FlightHub 2, enable automated inspection operations. Schedule an inspection task, and the DJI Dock 2 will automatically collect the data and upload the results to the cloud platform for further analysis and processing.
Remote drone deployment significantly reduces the workload on inspection personnel, supporting an easy-to-operate mode with centralized management of multiple docking stations.
Scheduled tasks facilitate a fully automated process, from flight operations to data transmission.
Designed to operate in harsh weather conditions, including extreme cold, heat, wind, rain, and dust, these systems ensure that inspections are completed on schedule and meet quality standards.
Drone Platform
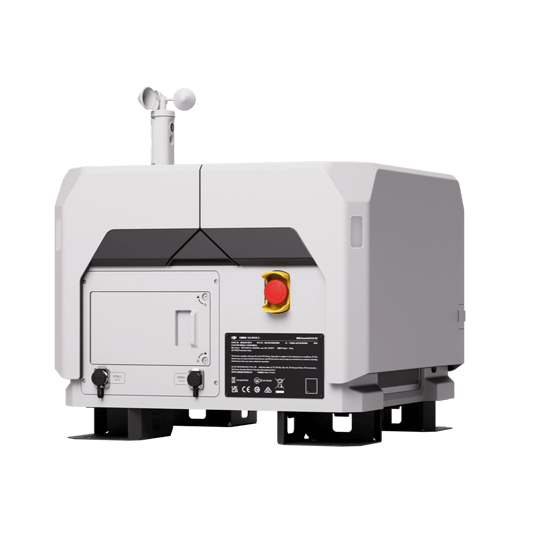
DJI Dock 2
... Open
Weight: 34 kg (without the drone).
Size: length 570 mm, width 583 mm, height 465 mm.
Environment adaptability: -25℃-45℃ working temperature, IP55 Rate, max operation height 4,000 m.
Max Operating Radius: 10 km.
Size: length 570 mm, width 583 mm, height 465 mm.
Environment adaptability: -25℃-45℃ working temperature, IP55 Rate, max operation height 4,000 m.
Max Operating Radius: 10 km.
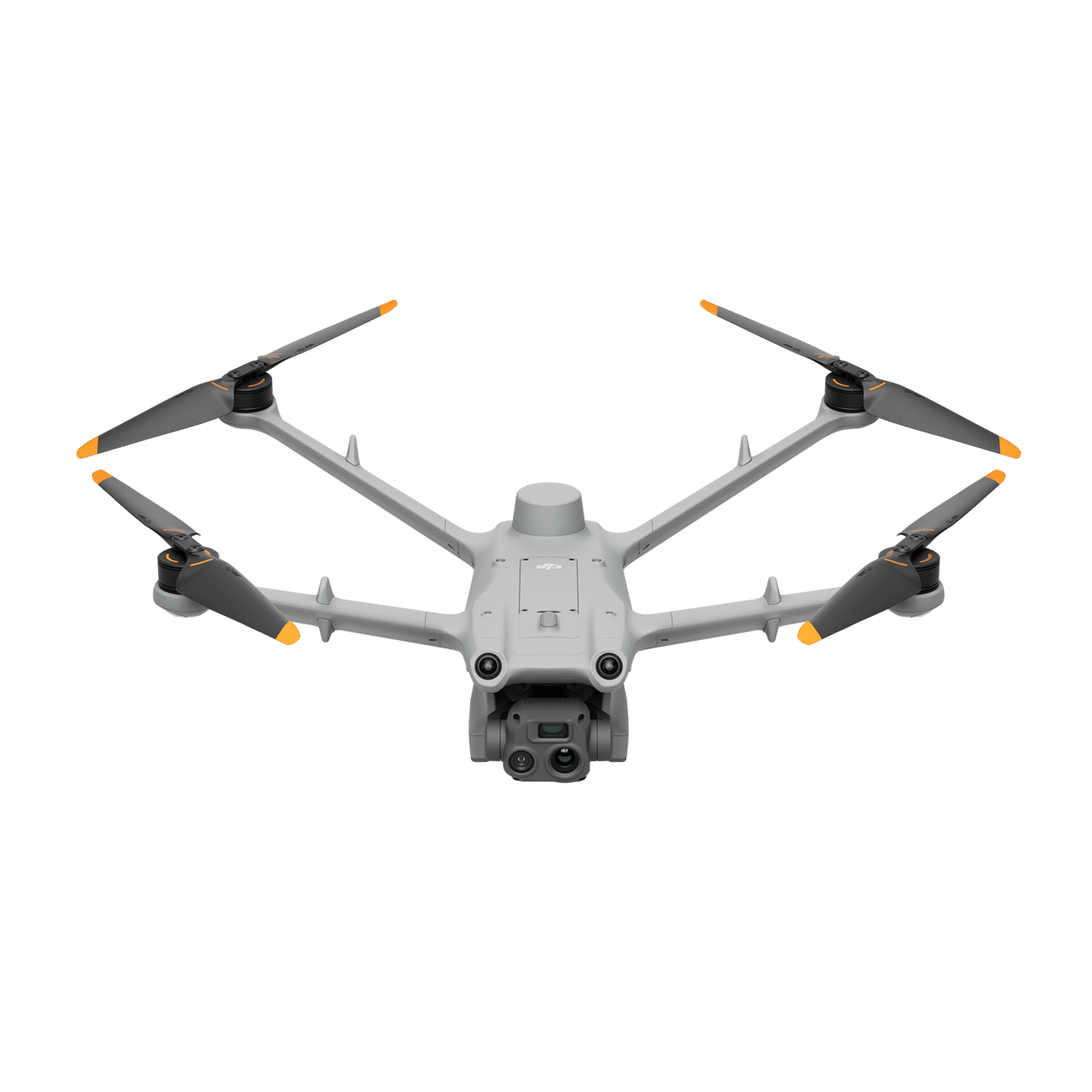
Matrice 3TD
... Open
Weigh: 1410 g.
Size: length 335 mm, width 398 mm, height 153 mm(without propellers).
Max flight time: 50 minutes.
Max Operating Radius: 10 km.
Wide camera: 1/1.32'' CMOS, 48MP.
Tele camera: 1/2" CMOS, 12MP.
Thermal camera: UHR Infrared Image Mode 1280 × 1024@30fps.
Environment adaptability: -25℃-45℃ working temperature, IP55 Rate, max operation height 4,000 m.
Size: length 335 mm, width 398 mm, height 153 mm(without propellers).
Max flight time: 50 minutes.
Max Operating Radius: 10 km.
Wide camera: 1/1.32'' CMOS, 48MP.
Tele camera: 1/2" CMOS, 12MP.
Thermal camera: UHR Infrared Image Mode 1280 × 1024@30fps.
Environment adaptability: -25℃-45℃ working temperature, IP55 Rate, max operation height 4,000 m.
Workflow
- Mission Planning:
- Use DJI FlightHub 2 to plan inspection routes based on high-definition 3D models of the substation.
- Or import previously saved inspection flight routes to the DJI FlightHub 2 via the Pilot 2 app using the Live Mission Recording feature. - Data Collection:
- Using DJI FlightHub 2, select the preferred dock and scheduled inspection mission.
- The Matrice 3TD will execute the inspection tasks according to the plan, and upload the captured data to DJI FlightHub 2. - Data Analysis:
- Analyze the images to detect defects or required maintenance work. Transfer the data to a third-party software to identify equipment defects using model detection.
Multipurpose Drone Inspection
The DJI Matrice 350 RTK is a reliable platform with interchangeable payloads tailored to meet the needs of specific tasks. From mapping to inspection, the Matrice 350 RTK provides comprehensive operational capabilities for inspection teams.
Equipped with a variety of payloads, it delivers operational efficiency and enhanced inspection capabilities.
Its longer flight time allows for prolonged operations in a single flight.
When paired with the Zenmuse L2, it enables high-density point cloud mapping to create precise models of substations.
When paired with the Zenmuse H30 Series, it offers high-definition zoom capabilities and a laser rangefinder, along with intelligent and precise re-shooting functionality, which greatly enhances the efficiency of aerial inspections.
Drone Platform
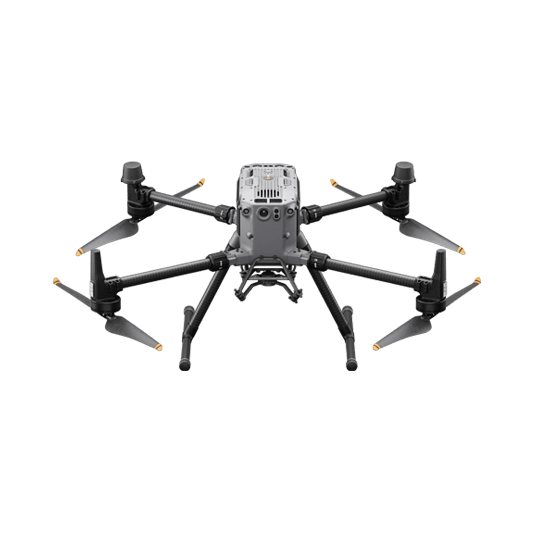
Matrice 350 RTK
... Open
Weight: Approx. 6.47 kg(with single downward gimbal and two TB65 batteries).
Max Flight Time: 55 minutes.
Sensing system: Six-directional sensing and positioning.
Environment Adaptability: IP55, Max Service Ceiling Above Sea Level 7,000 m (with 1676 propellers,without other payload); Max Wind Resistance 12 m/s.
Max Flight Time: 55 minutes.
Sensing system: Six-directional sensing and positioning.
Environment Adaptability: IP55, Max Service Ceiling Above Sea Level 7,000 m (with 1676 propellers,without other payload); Max Wind Resistance 12 m/s.
Payload And Software
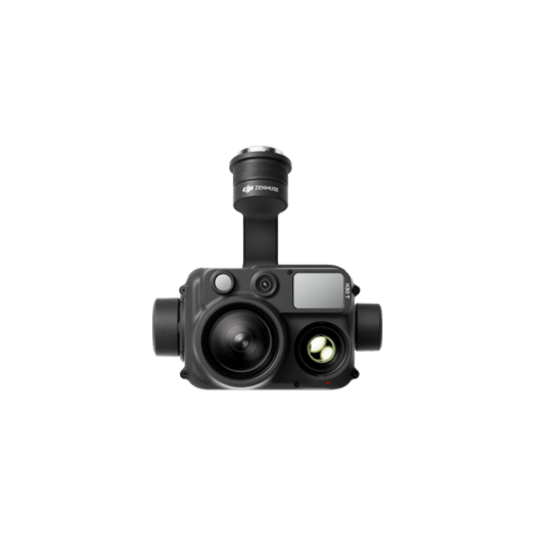
Zenmuse H30T
... Open
Weight: 920±5 g.
Ingress Protection Rating: IP54.
Zoom Camera: 1/1.8-inch CMOS, Effective Pixels: 40 MP.
Wide-Angle Camera: 1/1.3-inch CMOS, Effective Pixels: 48 MP.
Infrared Thermal Camera: 1280×1024@30fps.
Laser Range Finder: max range 3000 m.
Ingress Protection Rating: IP54.
Zoom Camera: 1/1.8-inch CMOS, Effective Pixels: 40 MP.
Wide-Angle Camera: 1/1.3-inch CMOS, Effective Pixels: 48 MP.
Infrared Thermal Camera: 1280×1024@30fps.
Laser Range Finder: max range 3000 m.
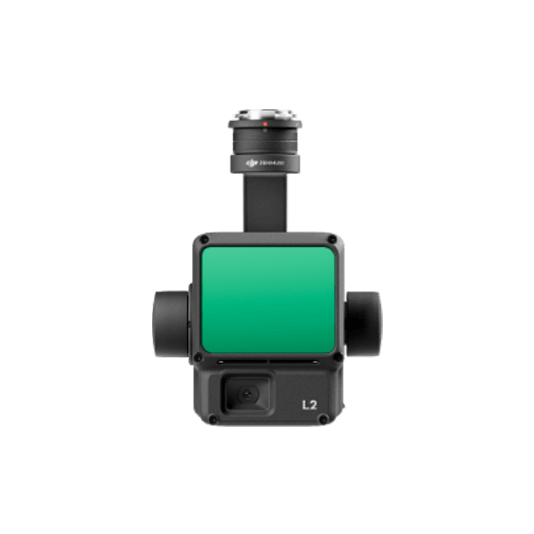
Zenmuse L2
... Open
Integrates frame LiDAR, a self-developed high-accuracy IMU system, and a 4/3 CMOS RGB mapping camera.
2.5 km2 covered in a single flight.
Detection Range 250m @10% reflectivity, 100klx.
Effective Point Cloud Rate: 240,000 pts/s.
Supports 5 Returns.
Turnkey Solution.
2.5 km2 covered in a single flight.
Detection Range 250m @10% reflectivity, 100klx.
Effective Point Cloud Rate: 240,000 pts/s.
Supports 5 Returns.
Turnkey Solution.
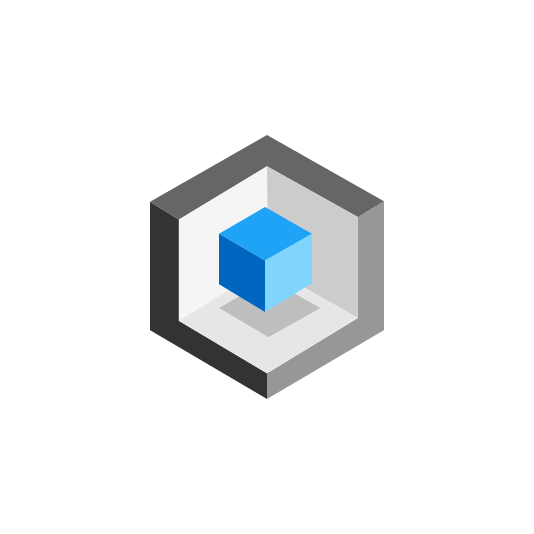
Workflow
- Substation Digital Twin:
- Use the DJI Pilot 2 app and Matrice 350 RTK equipped with the Zenmuse L2 to generate a 3D model using the mapping mission functions.
- Import the data into DJI Terra to generate the LiDAR point cloud of the substation. Use the model to plan expansion and maintenance work. - Thermal Inspection Mission:
- Using the Matrice 350 RTK equipped with the Zenmuse H30T payload, manually fly to capture thermal readings of the key components of the substation. Use the Live Mission Recording feature to easily repeat the same missions in the future. - Data Analysis:
- Analyze the inspection photos manually or use model detection to identify defects in the transmission corridor.